
Abstract
The objective of this report is to outline the design process and results of a thermal conduction module (TCM) originally designed by IBM for multi-chip modules (MCM). Chips soldered to the bottom of the module produce an incredible amount of heat because of their close proximity to one another, so a cooling plate must be designed to protect the circuitry. Water at 15 degrees Celsius flows through channels in the aluminum cooling plate (as shown in figure X) which removes heat from the system. The purpose of this project is to optimize the design of the cooling plate in order to minimize the maximum temperature of the cooling plate while maintaining a high heat transfer rate needed to dissipate collected heat.
Four main specifications of the system must be evaluated and designed; these include the volumetric flow rate of the water, the height of the centerline of the channel above the bottom of the cooling plate, the distance of the vertical symmetry lines away from the center of the channel, and the shape of the actual channel. Since multiple parameters must be designed and optimized simultaneously to produce the most effective system, the group’s design approach was to test each variable independently to find a qualitative correlation between their value and the temperature of the cooling plate. The group systematically used parametric modeling techniques to evaluate the maximum temperature of the plate if only a single variable was changed at a time.
The first parameter optimized was the volumetric flow rate, in which the group assumed a shape of the channel then test for varying volumetric flow rates. The second specification optimized was the width of the aluminum section surrounding the channel, followed by an optimization of the ideal height. Finally when the ideal position of the channel was determined, the ideal geometry and consequent dimensions of the channel were evaluated. The group concluded that, given the choice for an alternative, the ideal values and geometry for the best design are:
Volumetric flow rate = 7E-5 m3/s
a = 11mm
b = 9mm
Shape: Circle
Channel Diameter: 4mm
Although the Module was to contain rectangular channels, the group found a better design as it freed itself from the geometrical constrain to test about different shapes and ultimately found one which could in theory be easier to manufacture while performing better than the spaced rectangular channel. As the numerical and parametric calculations will show, the placement of the channel plays an important role on its capacity to dissipate heat. Outside our range of assumptions however, the group found that unlike what was expected, there is a strong correlation with the decrease of area of the channel and its ability to cool down the plate. Along with the design, the group will also demonstrate the ability to numerically model the temperature gradients within the aluminum cooling plate, as well as analytically solve for the heat transfer coefficient h within the channel while keeping in mind the constrains set forth in the given project.
Tony Kauffmann, Oscar Segovia
Stevens Institute of Technology-Heat Transfer
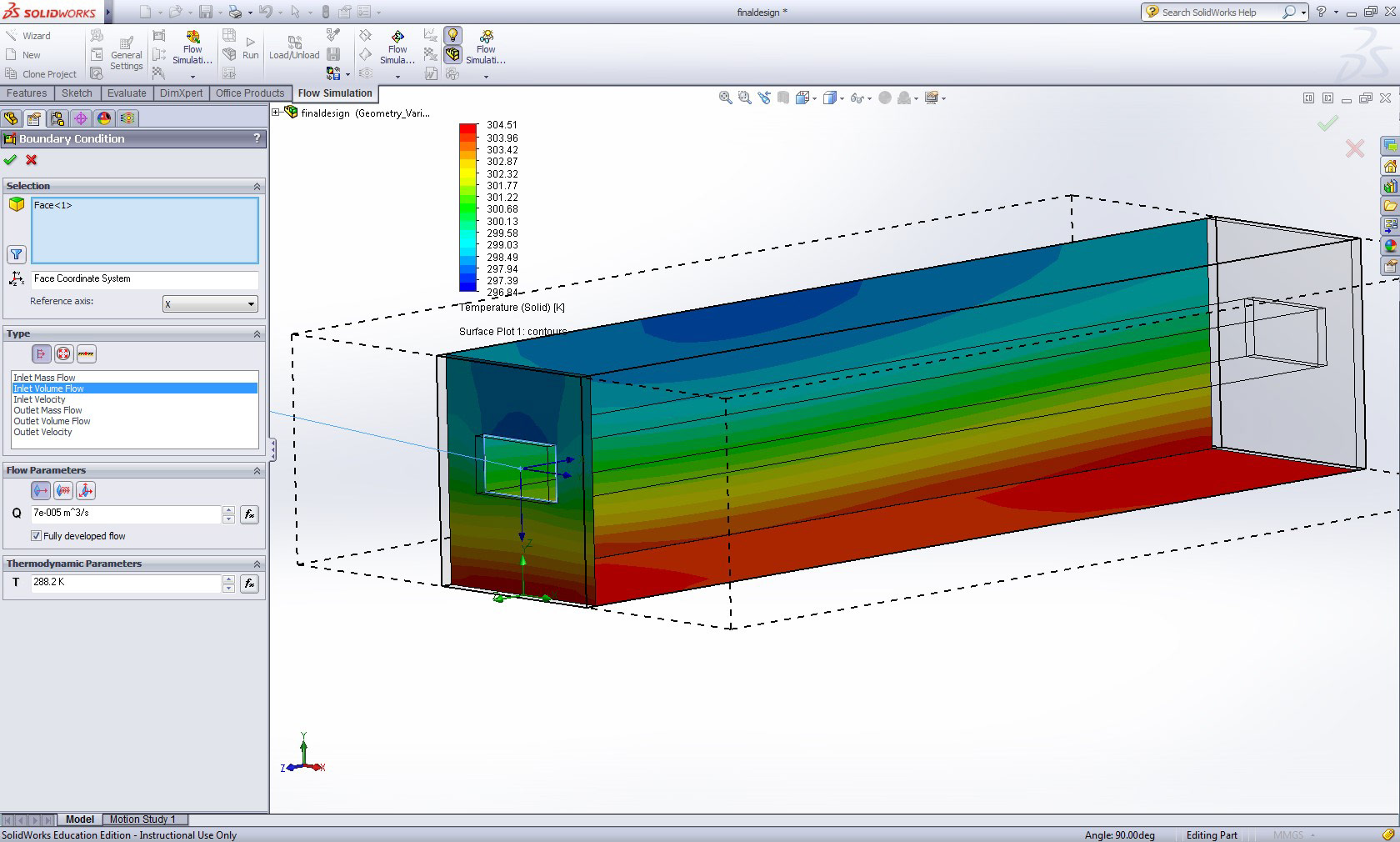

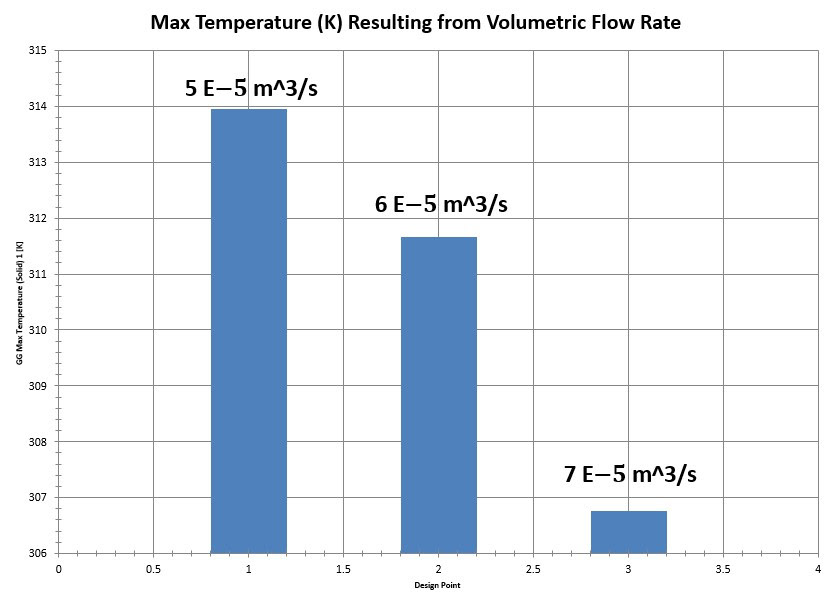
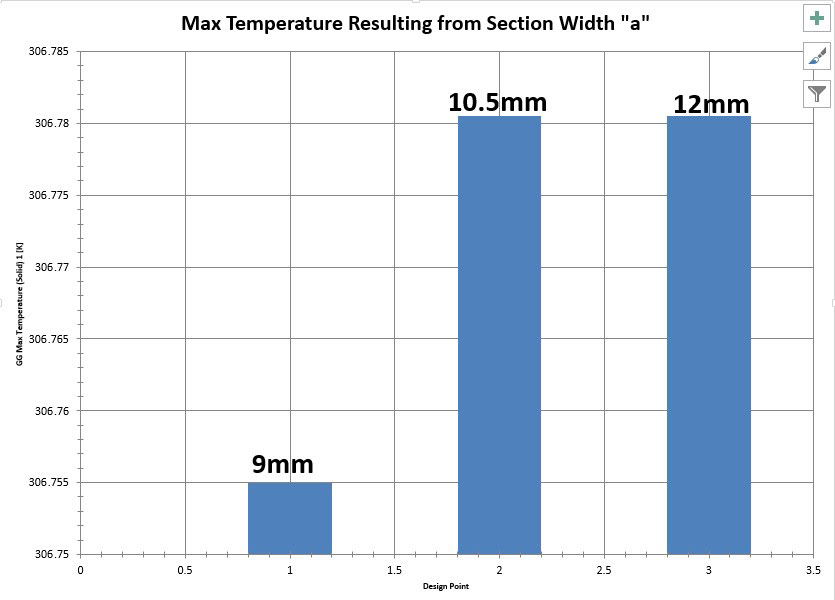
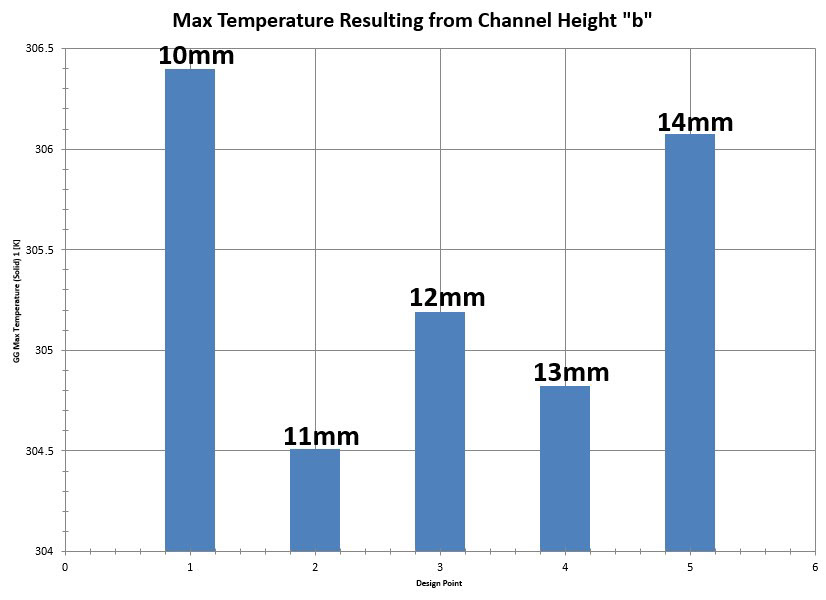
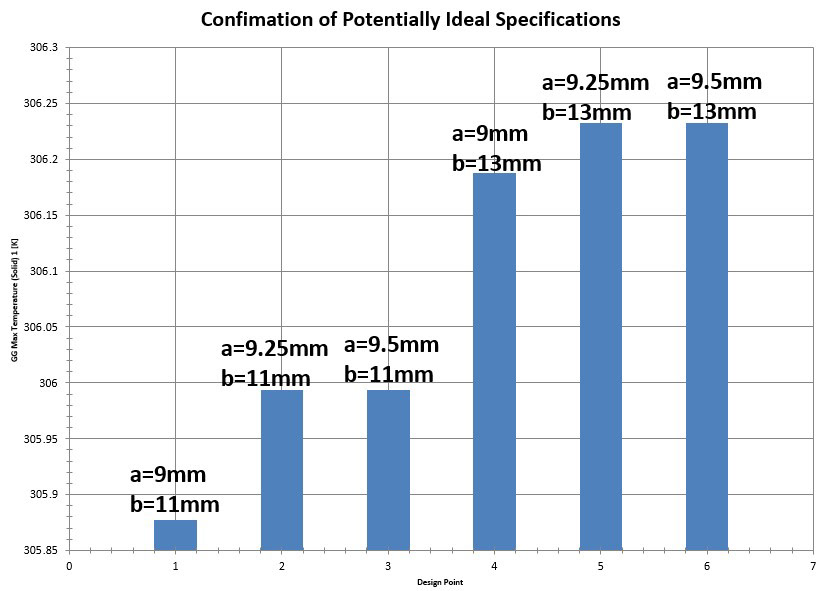
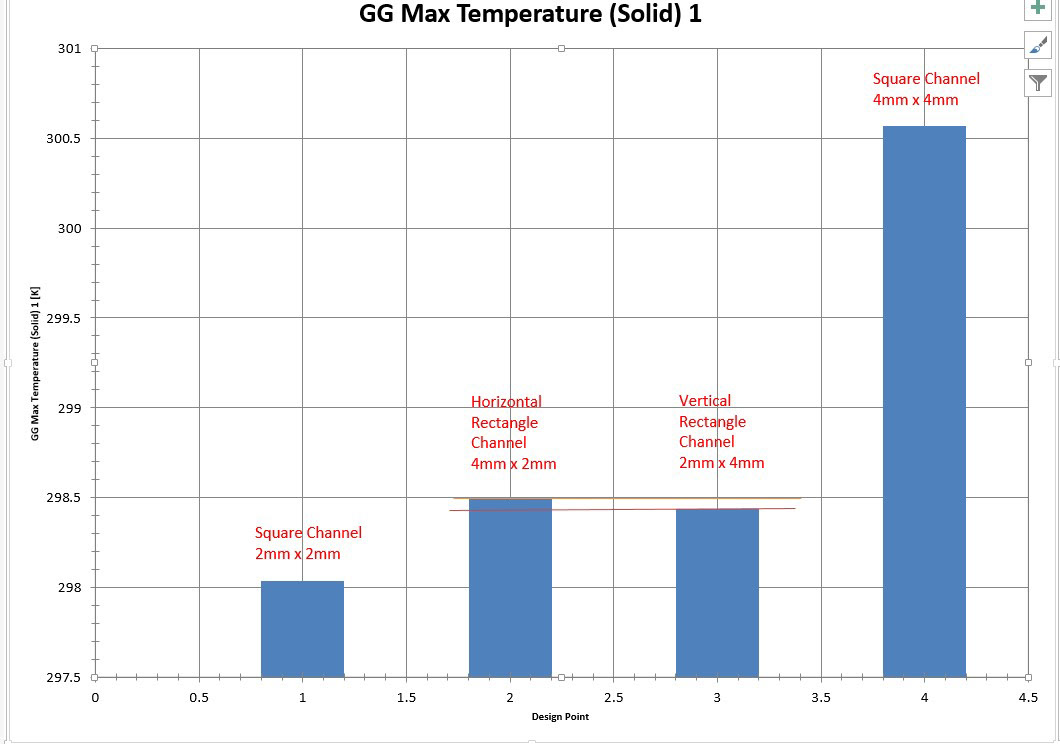


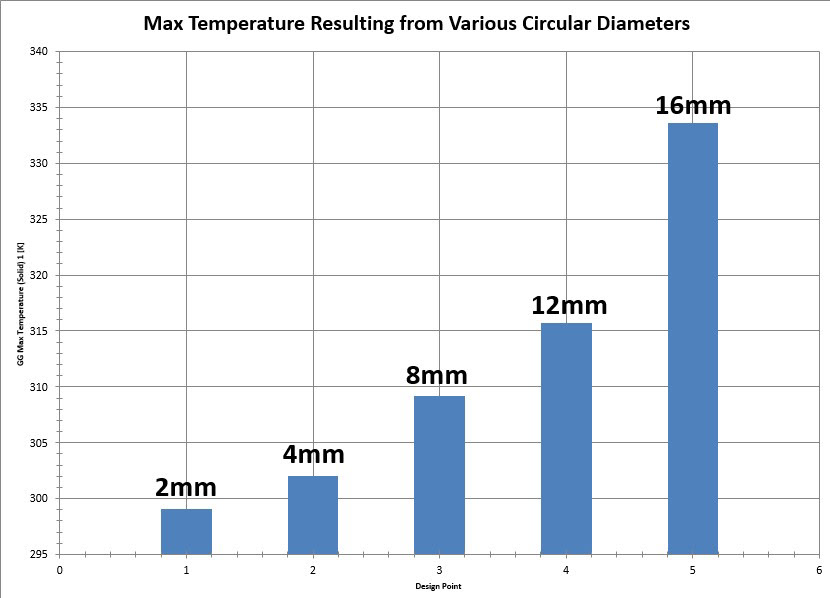
