UAV MECHANISMS, COMPONENTS AND INTEGRATION
Skill: Solidworks, Fusion 360, RTV Silicon mold making, CNC, Laser Cutter, 3d Printing.
The design of Autonomous Unmanned Aerial Vehicles, also known as Drones, requires multiple subsystems integration and careful attention to detail. Due to weight and size constrains, which ultimately impact performance and energy economy necessary for long range flights, creative solutions are necessary. As a result, composites such as fiber glass and carbon fiber* are extensively utilized in the material selection. This creates a challenging environment for design engineers as the creation of structural components and mechanisms requires different methods for prototyping and fitting than those of conventional metals or plastic based vehicles.
The use of Additive Manufacturing technology has allowed us to iterate rapidly through the process and strike upon solutions best suited for the business plan at hand; a business based in real-time Geo Surveillance, Mapping, Sensing and Analysis.
As a member of EAA (Experimental Aircraft Association), I receive a monthly publication titled SportAviation. While reading through the latest issue I stumbled upon an article called "The Competitive Edge - Team Chambliss's Pursuit of Peak Performance". I was impressed to see similar iterative skills and techniques used in our project, being utilized by one of the best engineers in the aviation field, Paulo Iscold. The article, which revolves around the RBAR race plane competition, dives deep into the methods of gaining a competitive edge through modifications to a standard Lycoming Thuderbolt AEIO-540-EXP manufactured by Zivko Aeronautics. Although the actual modifications are "carefully guarded secrets", I found the iterative process in such a fast paced environment refreshing. Similar to our approach, the use of CAD such as Solidworks, 3d scanning and CNC to create molds are used. In addition, water jet, laser cutters and 3d printers are something that we run 24/7 when necesary to keep parts moving towards optimal fit and function. Along side we have found creative solutions in RTV mold making.
A picture is worth 1000 words, so I leave you with some of my work as a visual story.
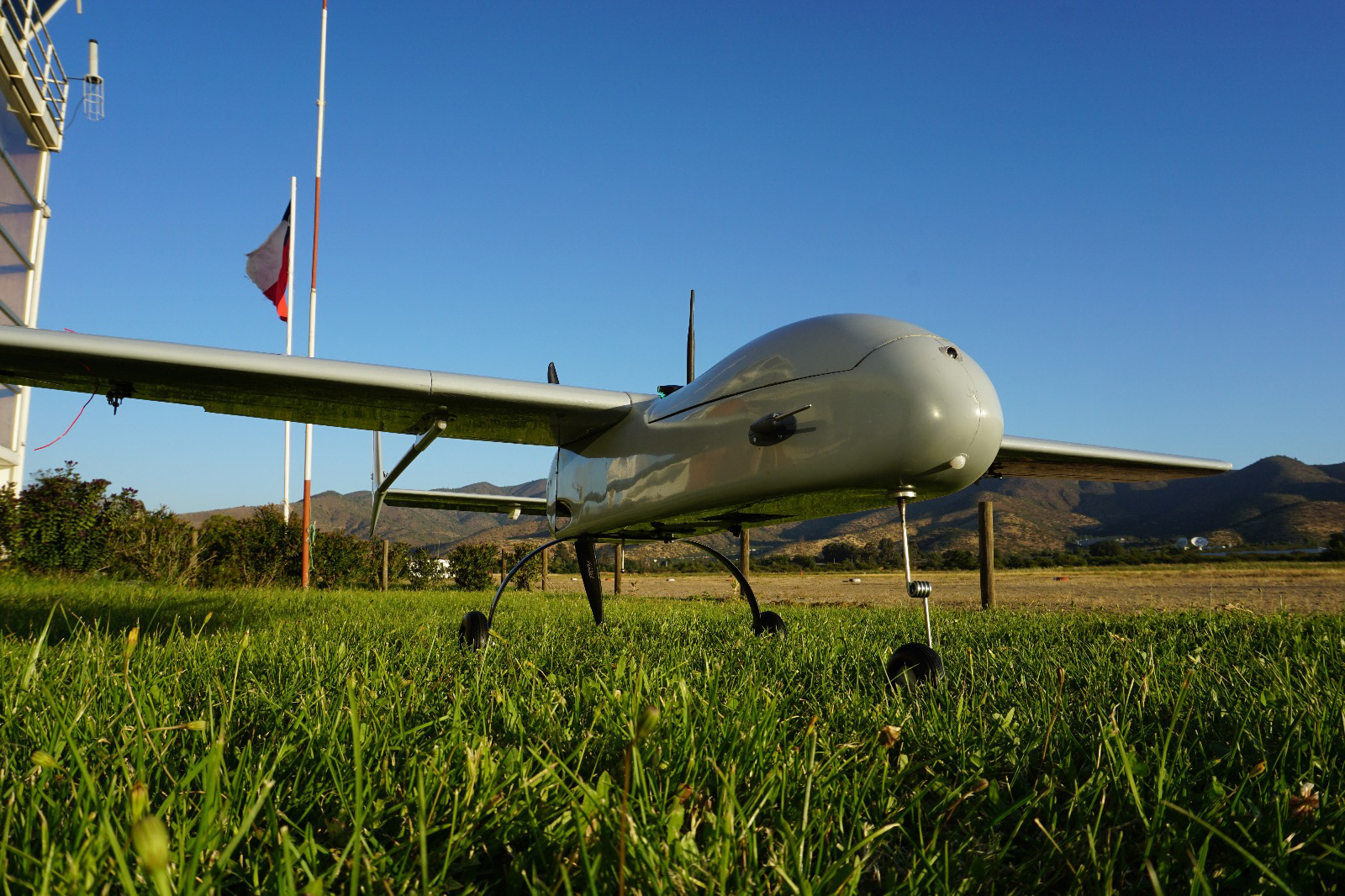
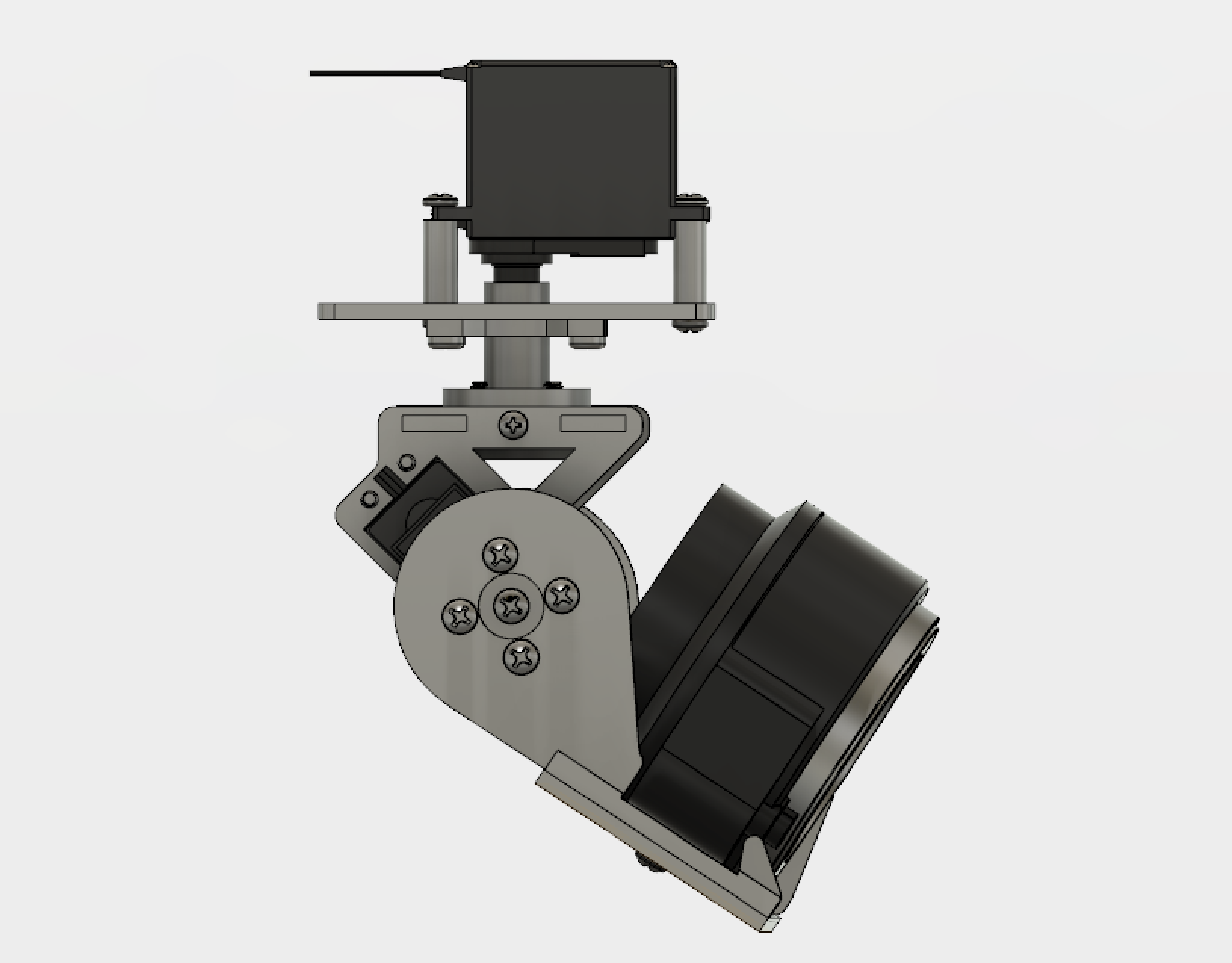
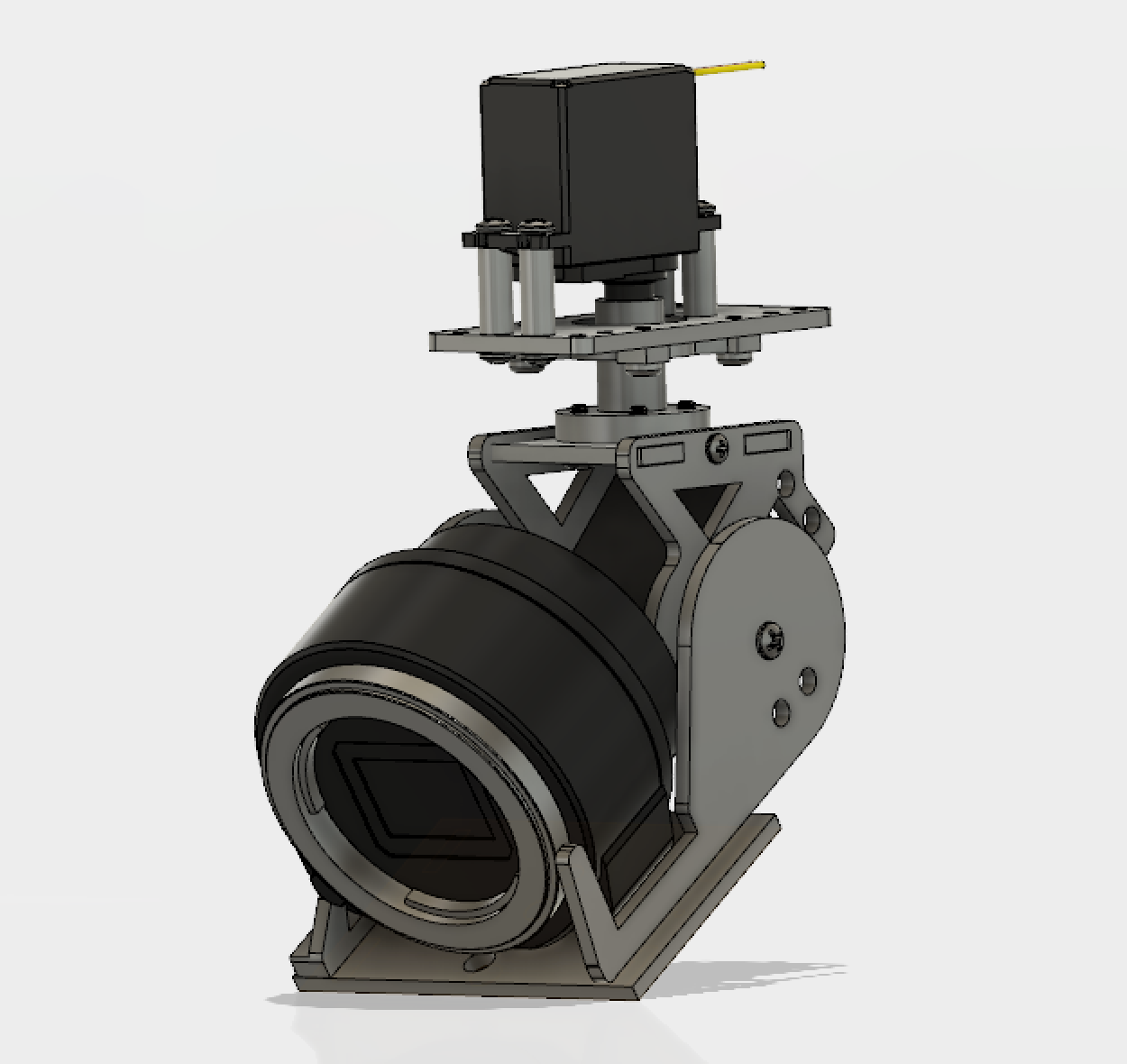
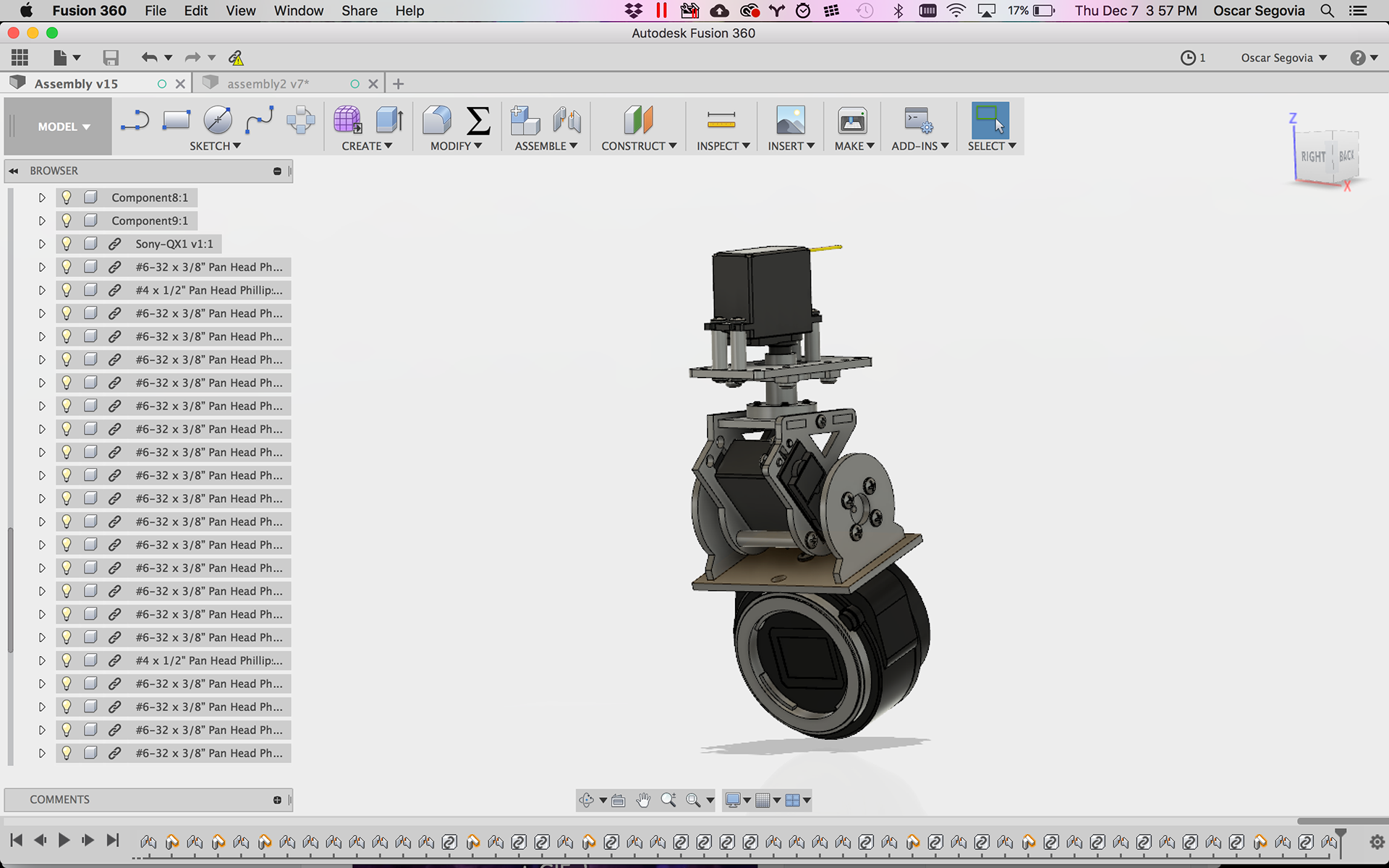
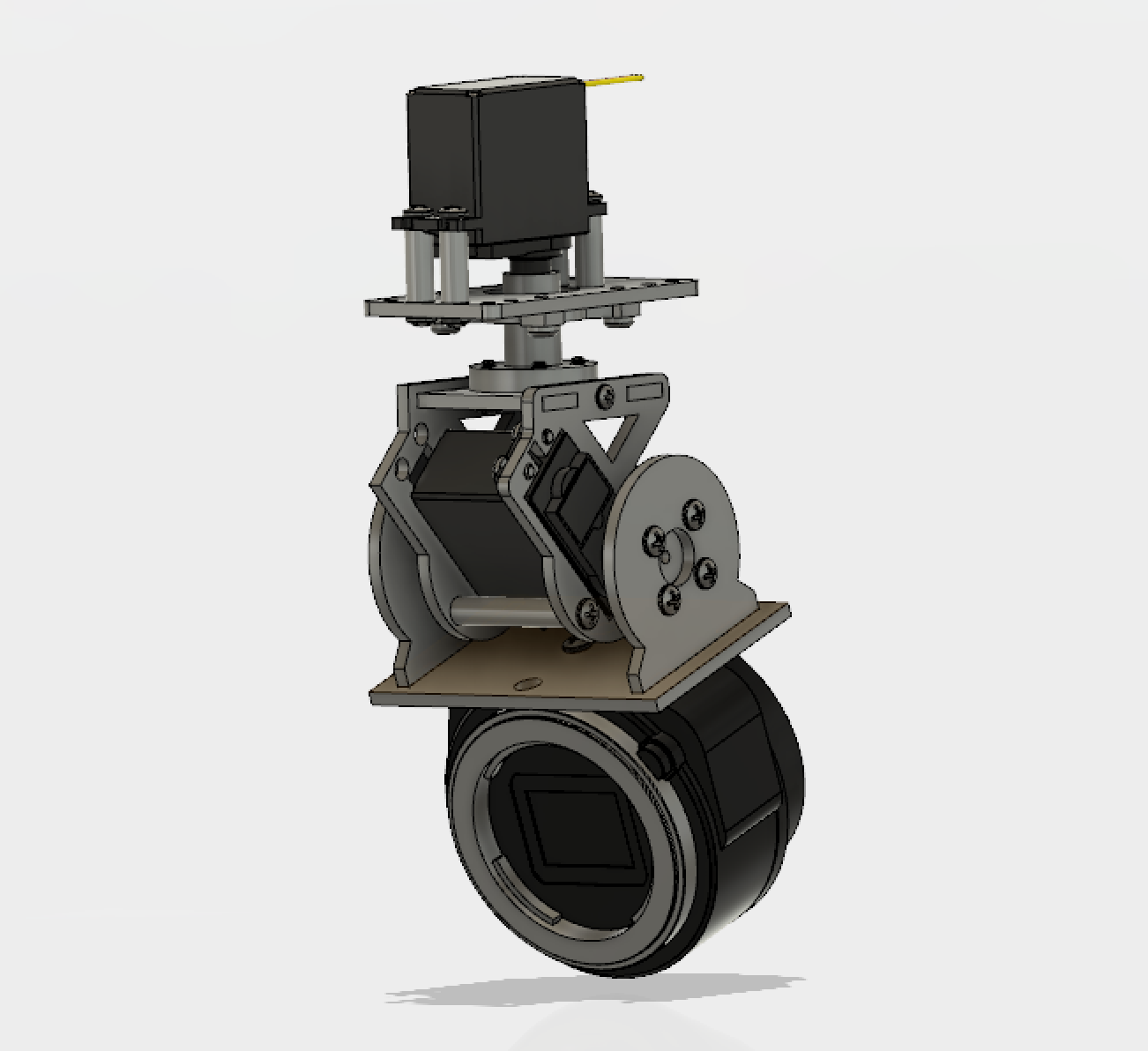
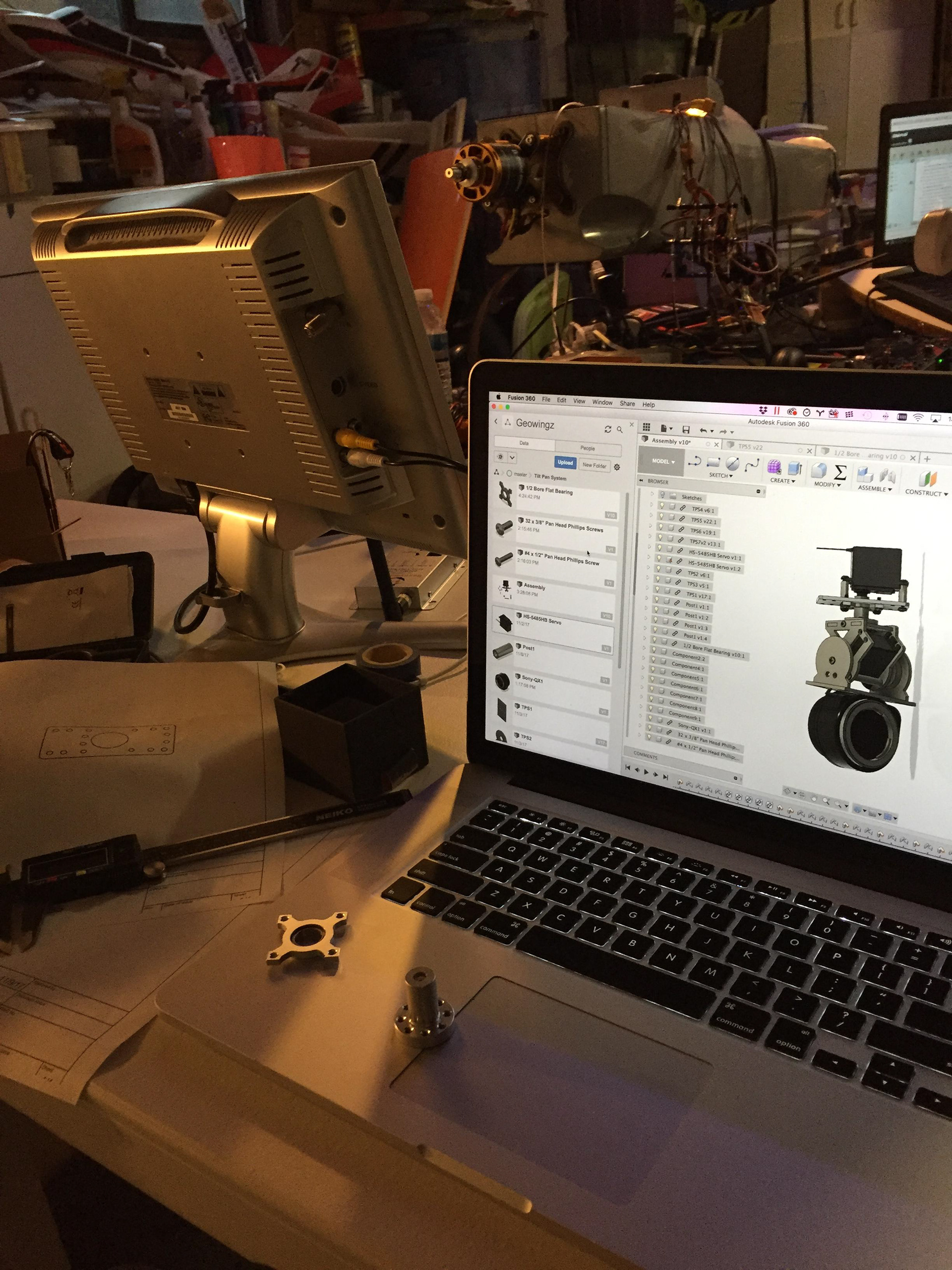
Re-engineering and modification of Pan Tilt System
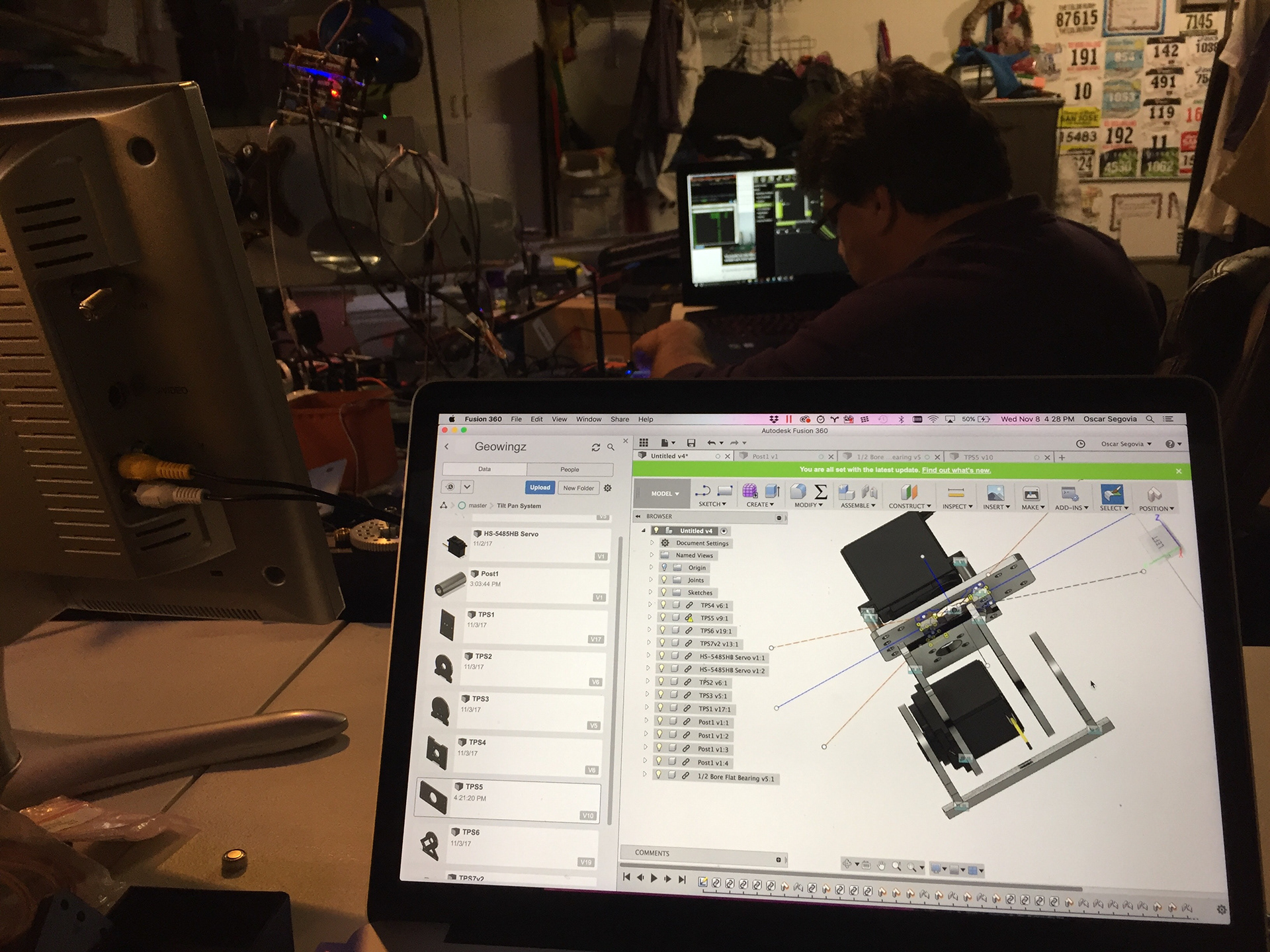
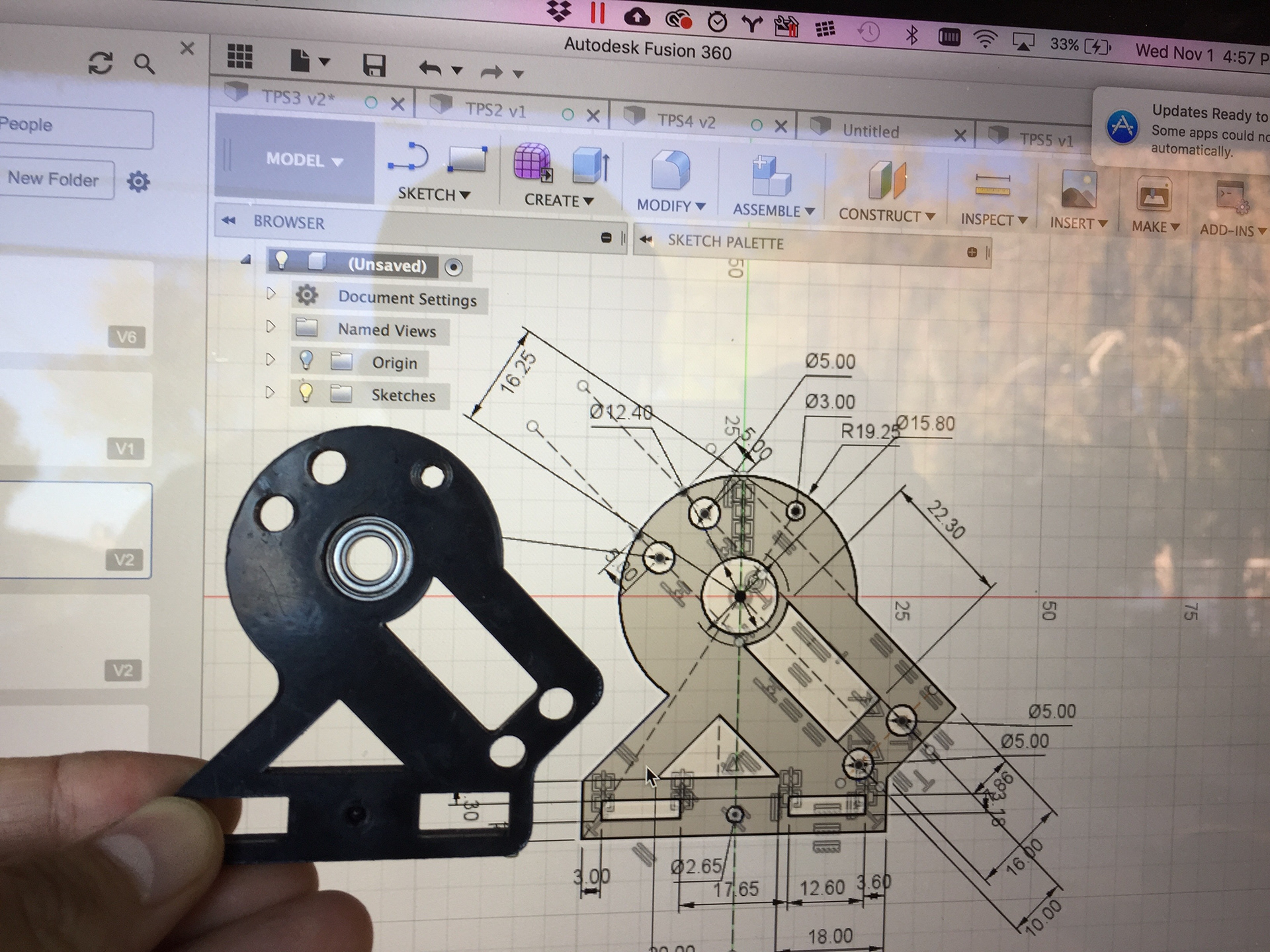
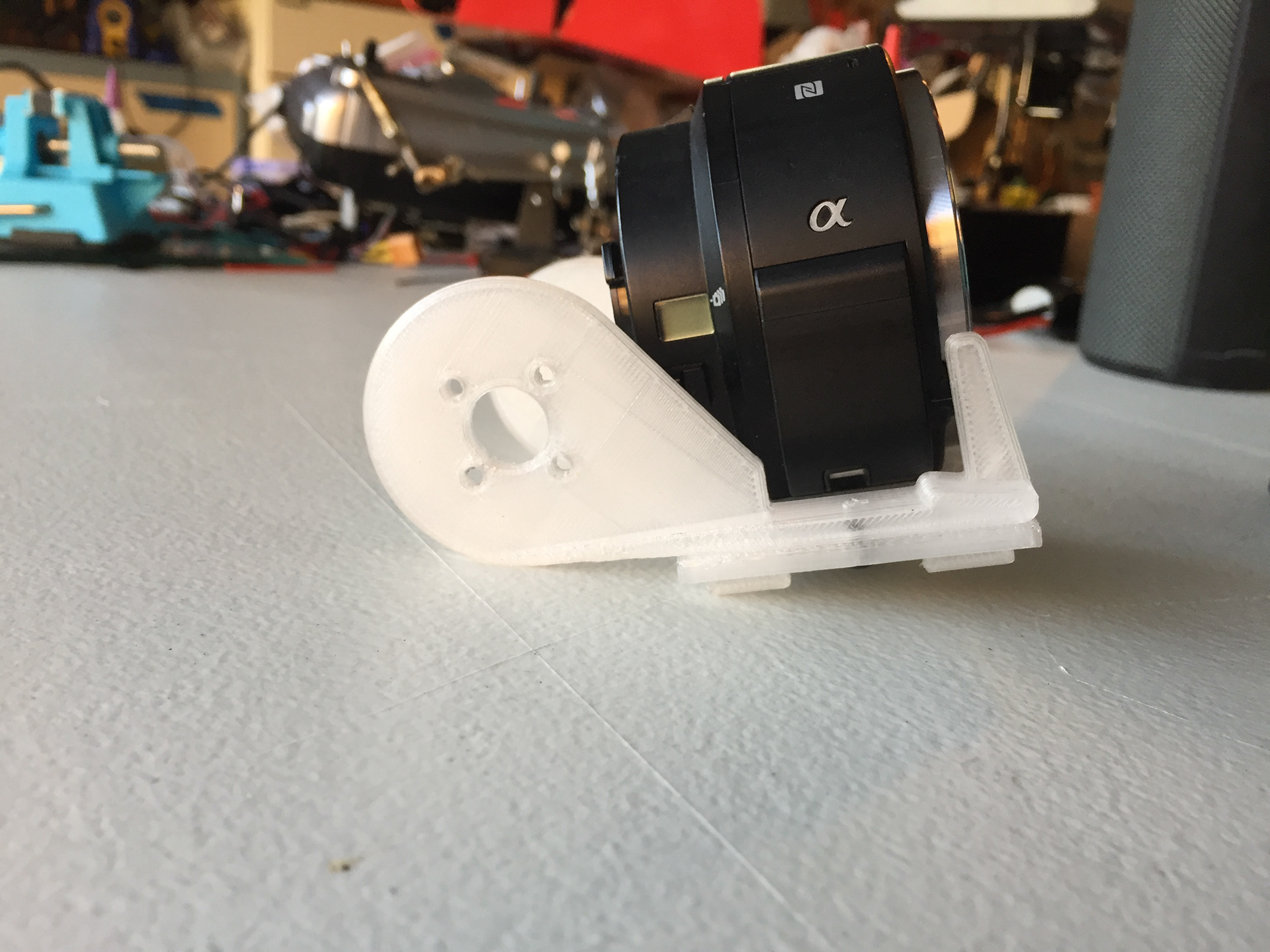
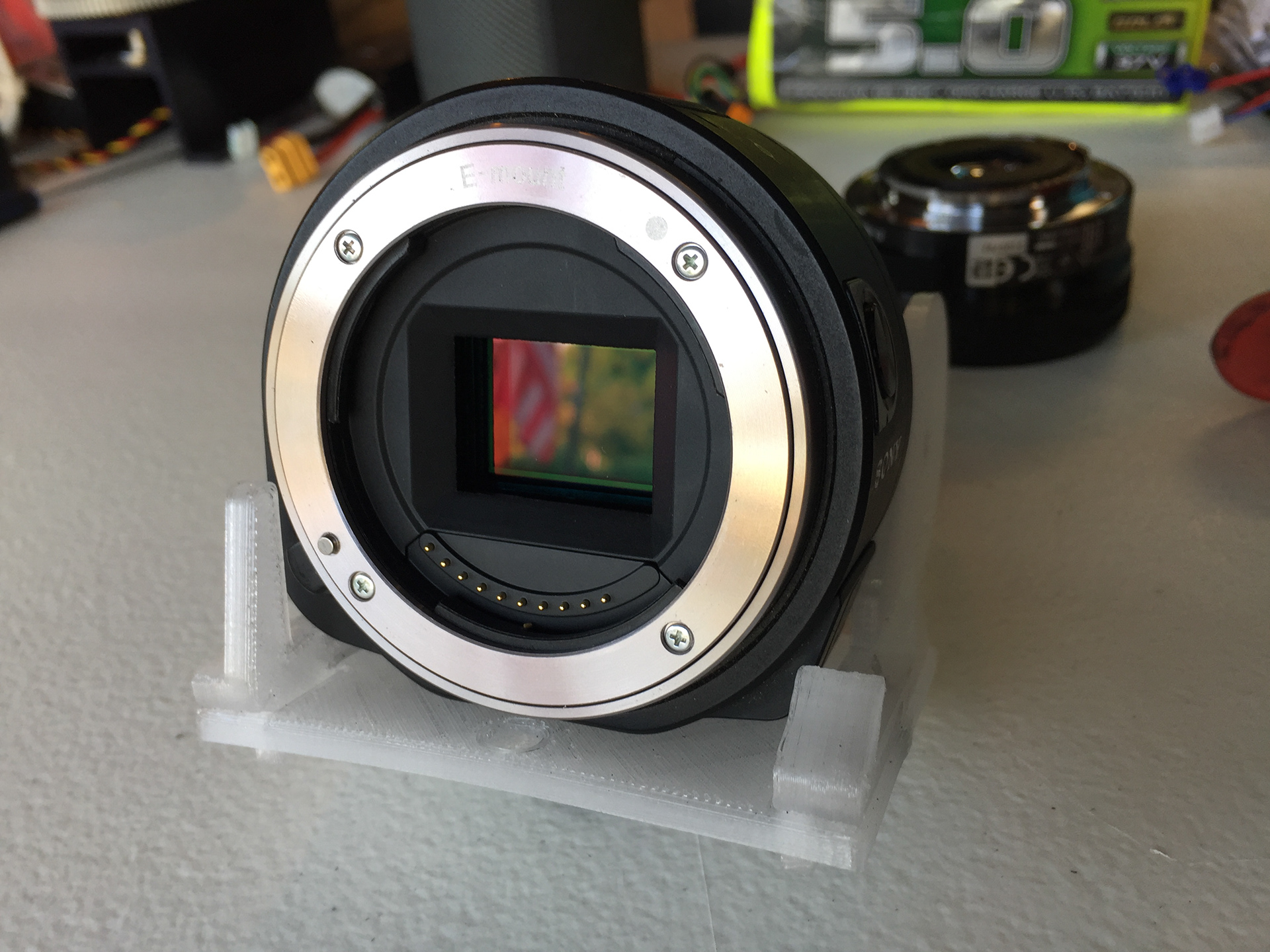
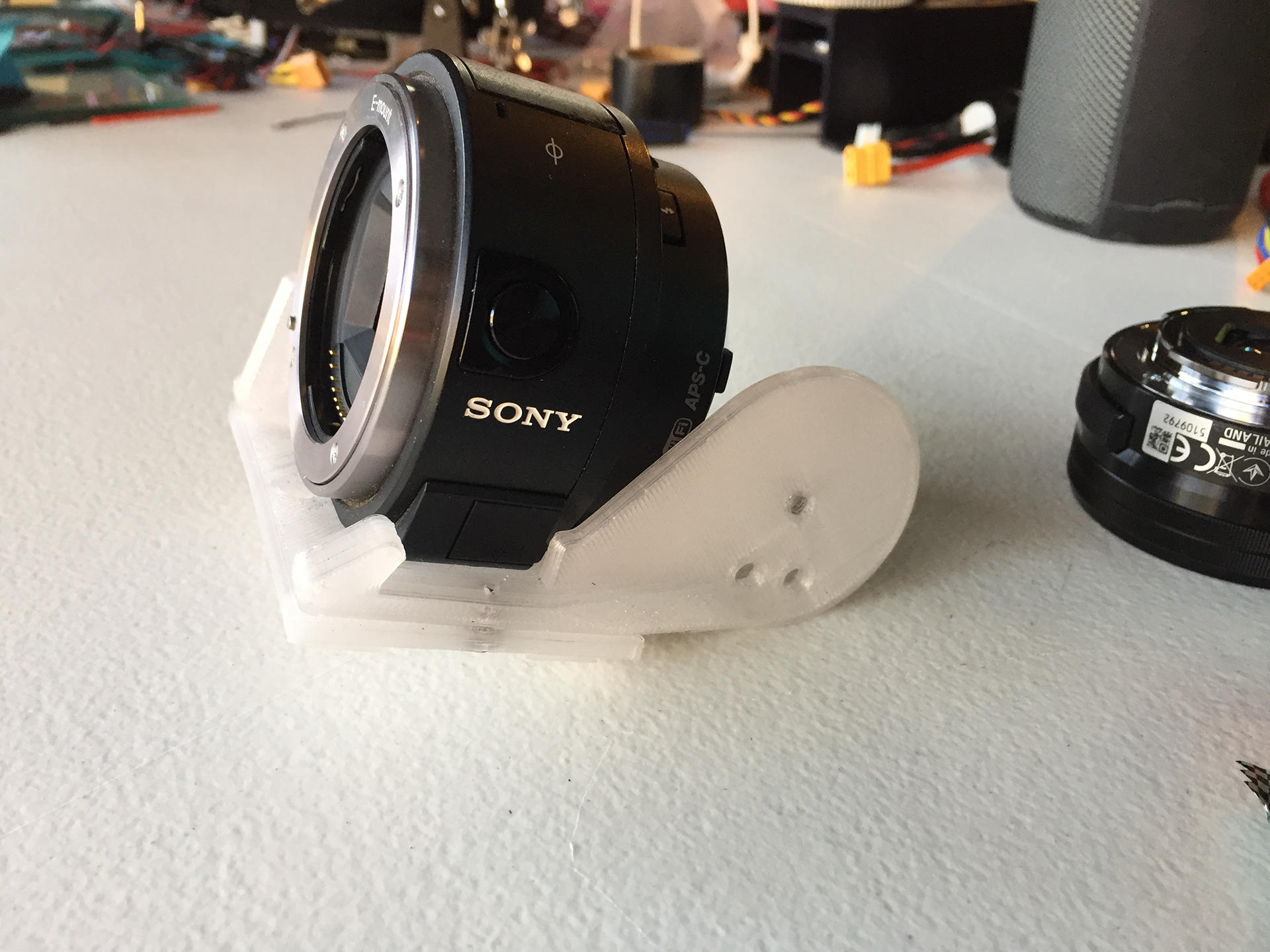
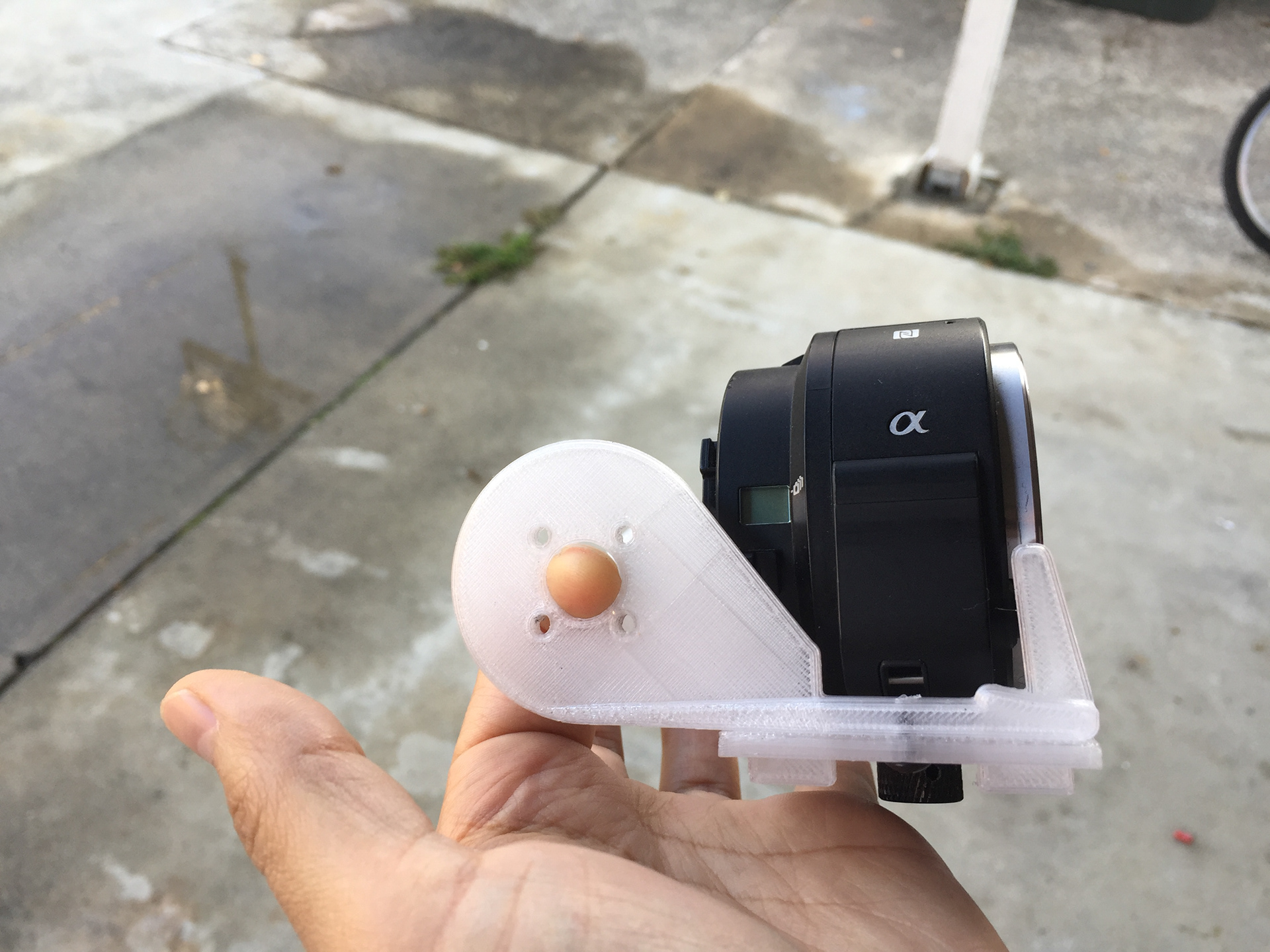
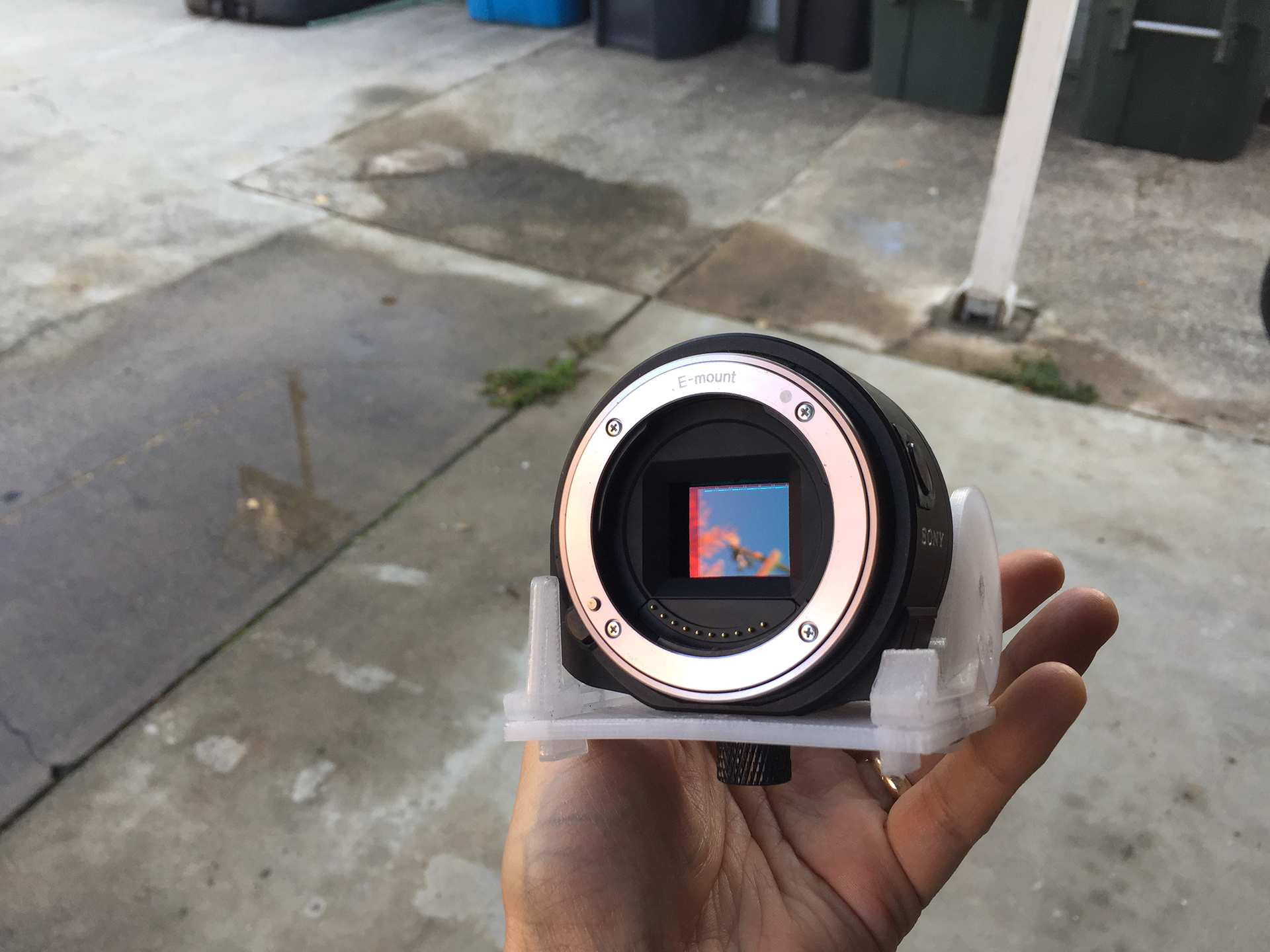
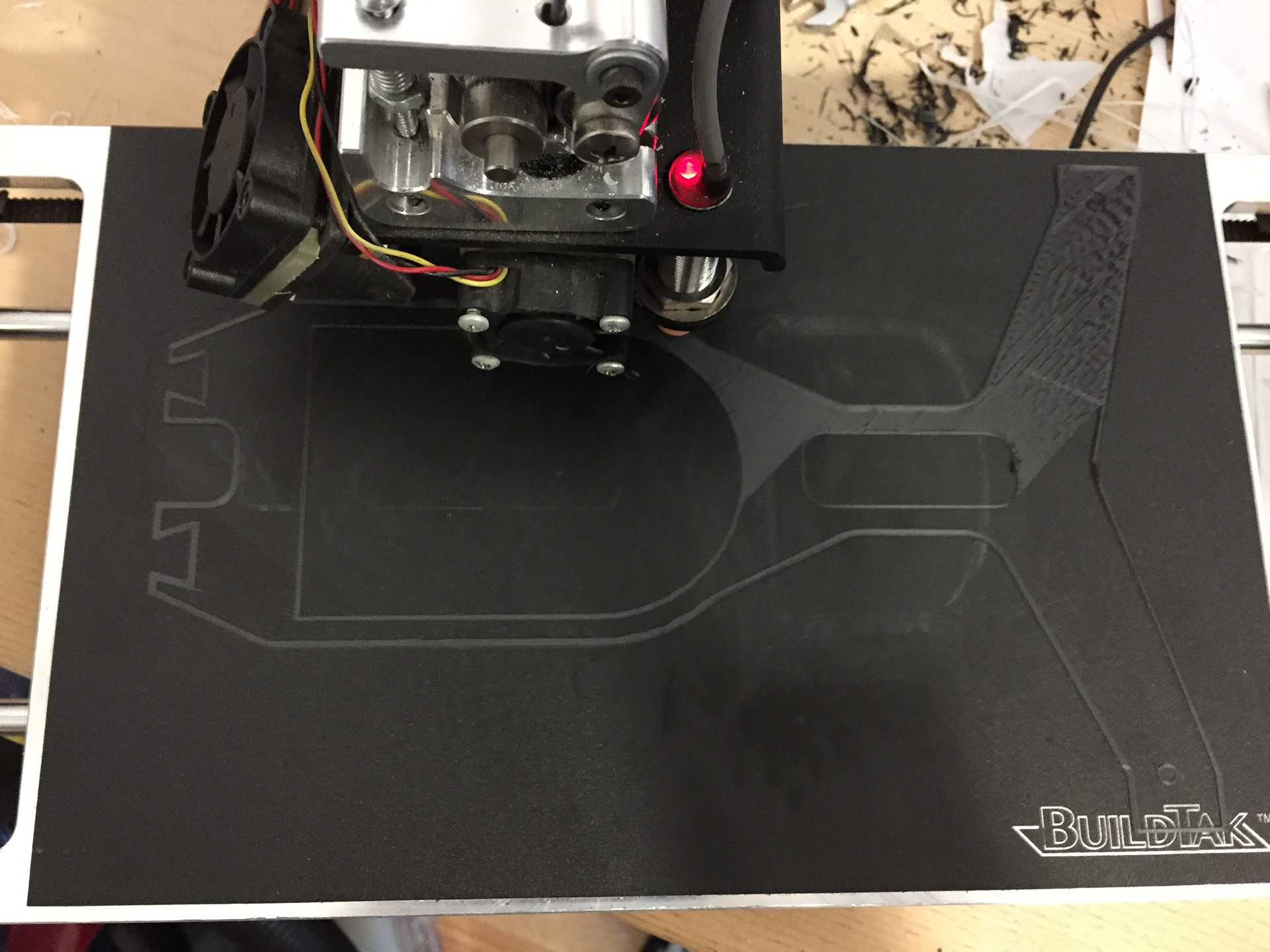
3D printing in Carbon Fiber
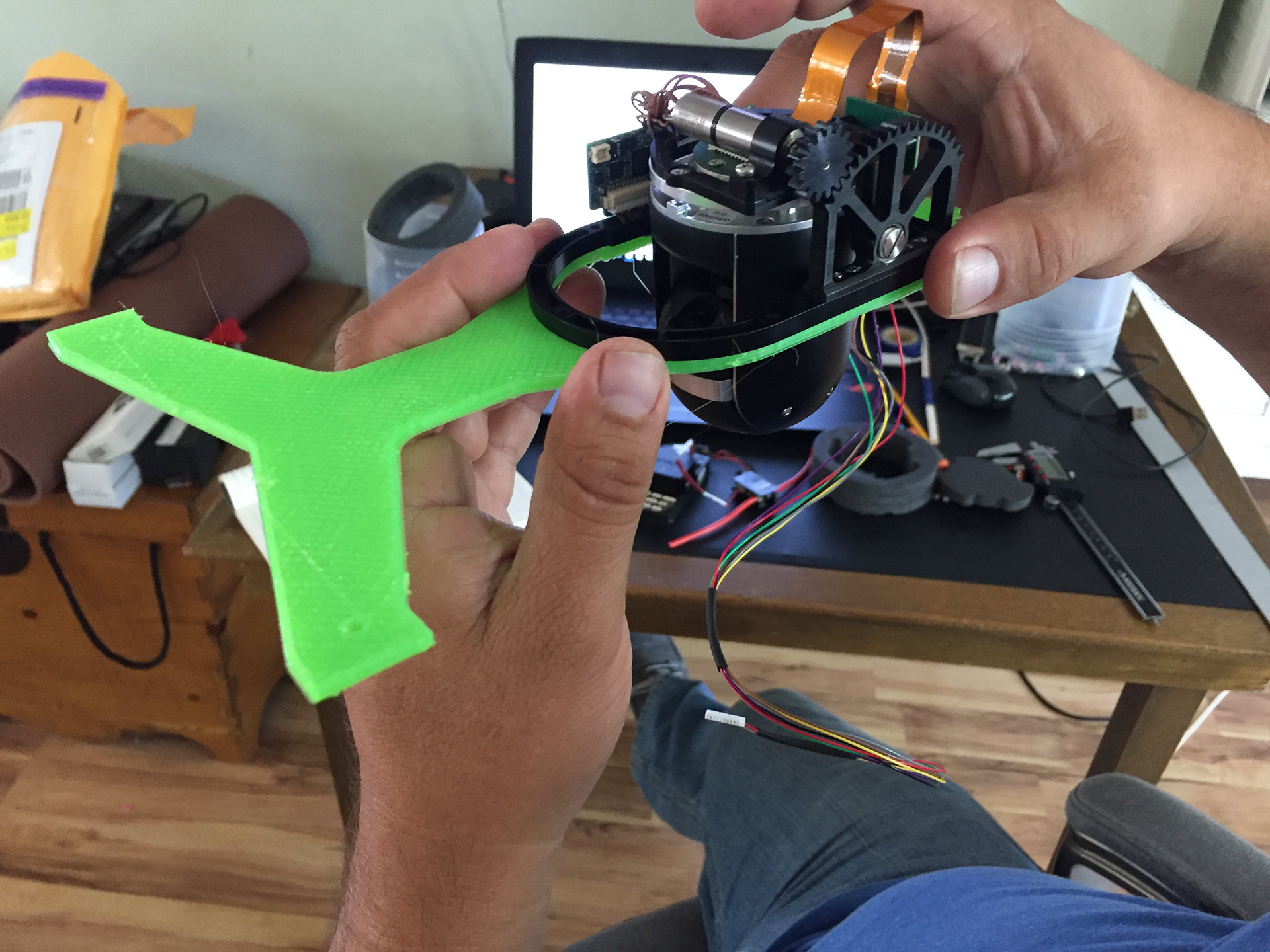
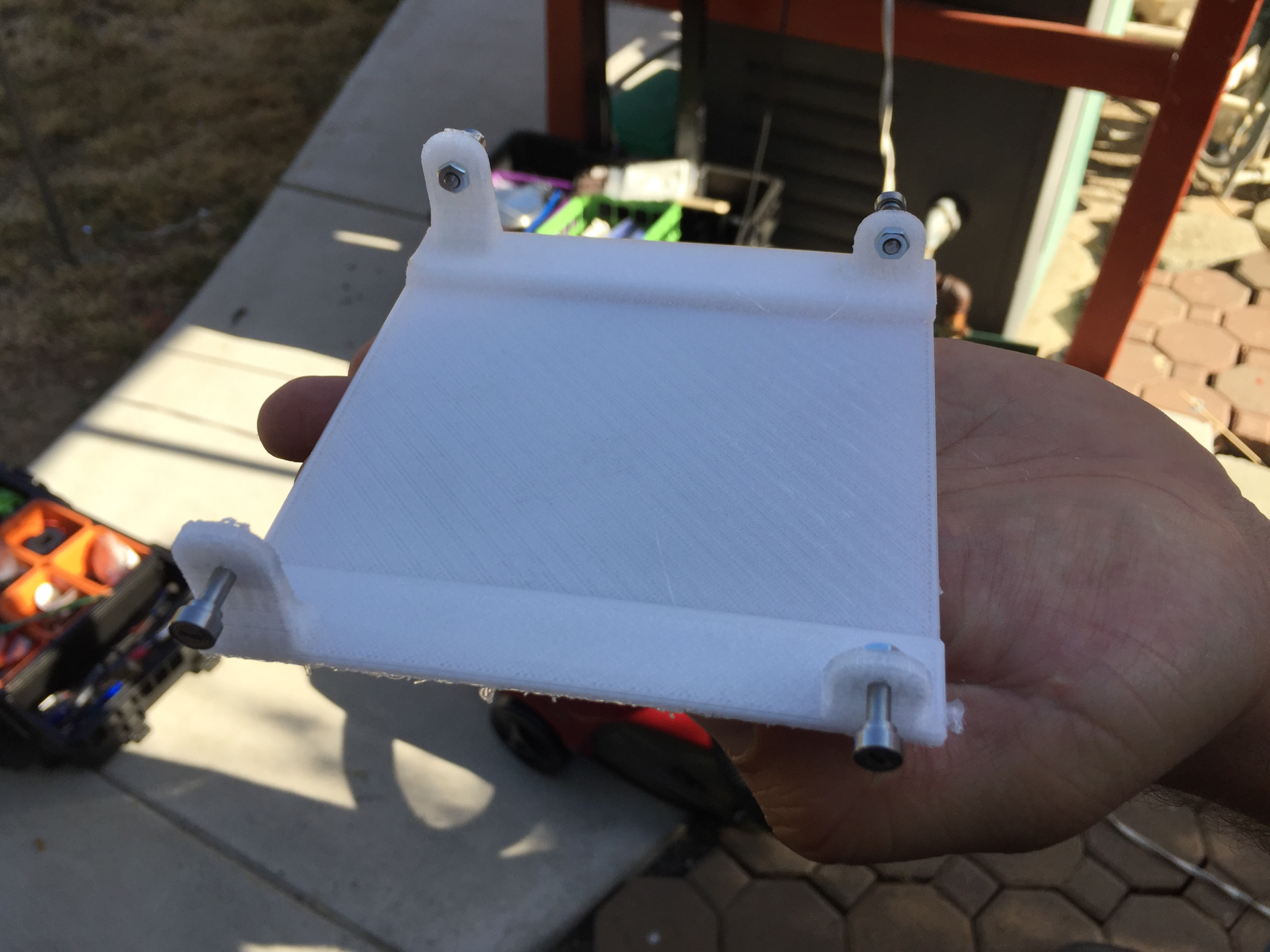
Sliding Door Design Iteration
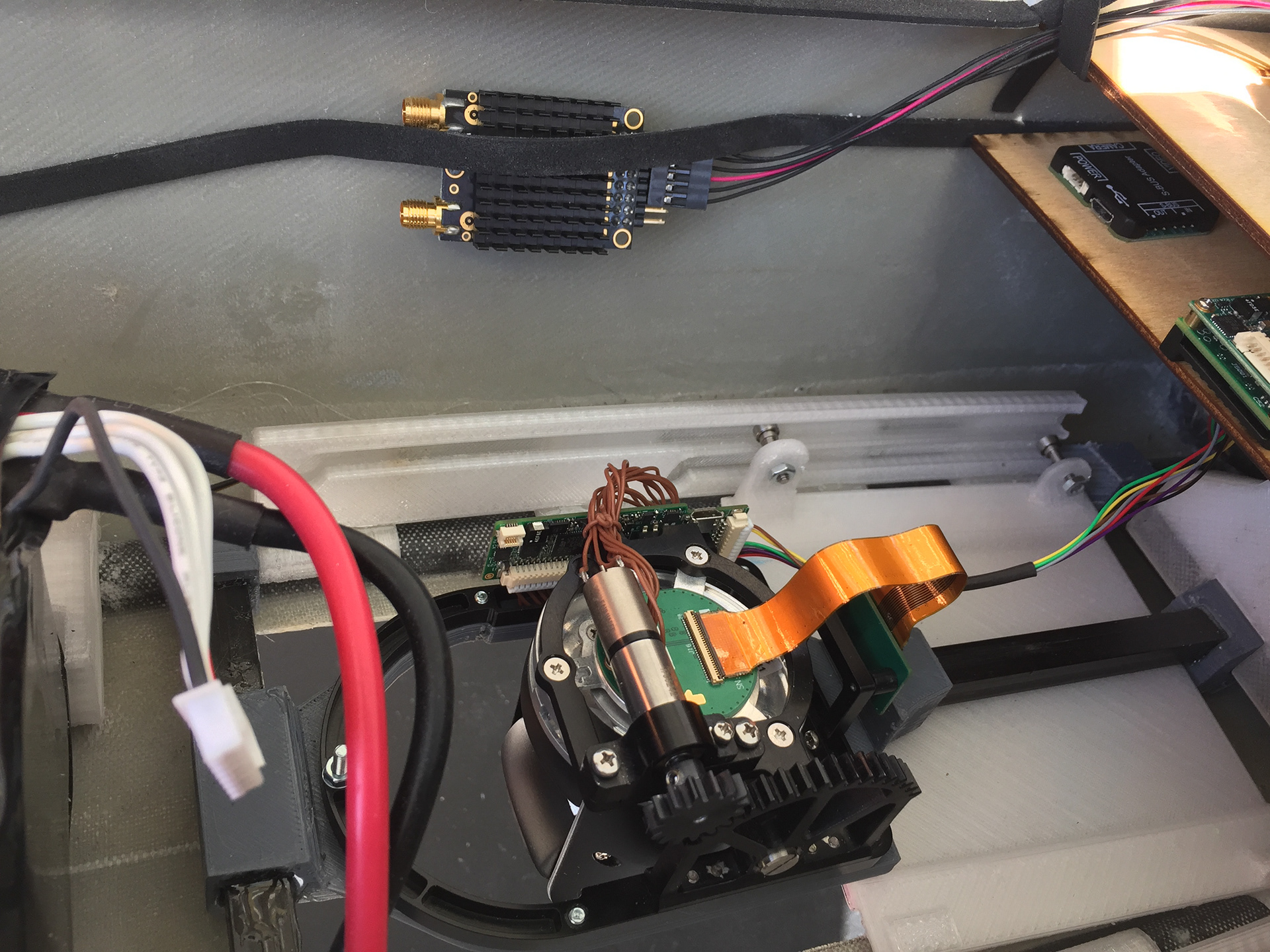
Cam + Door mechanism assembly
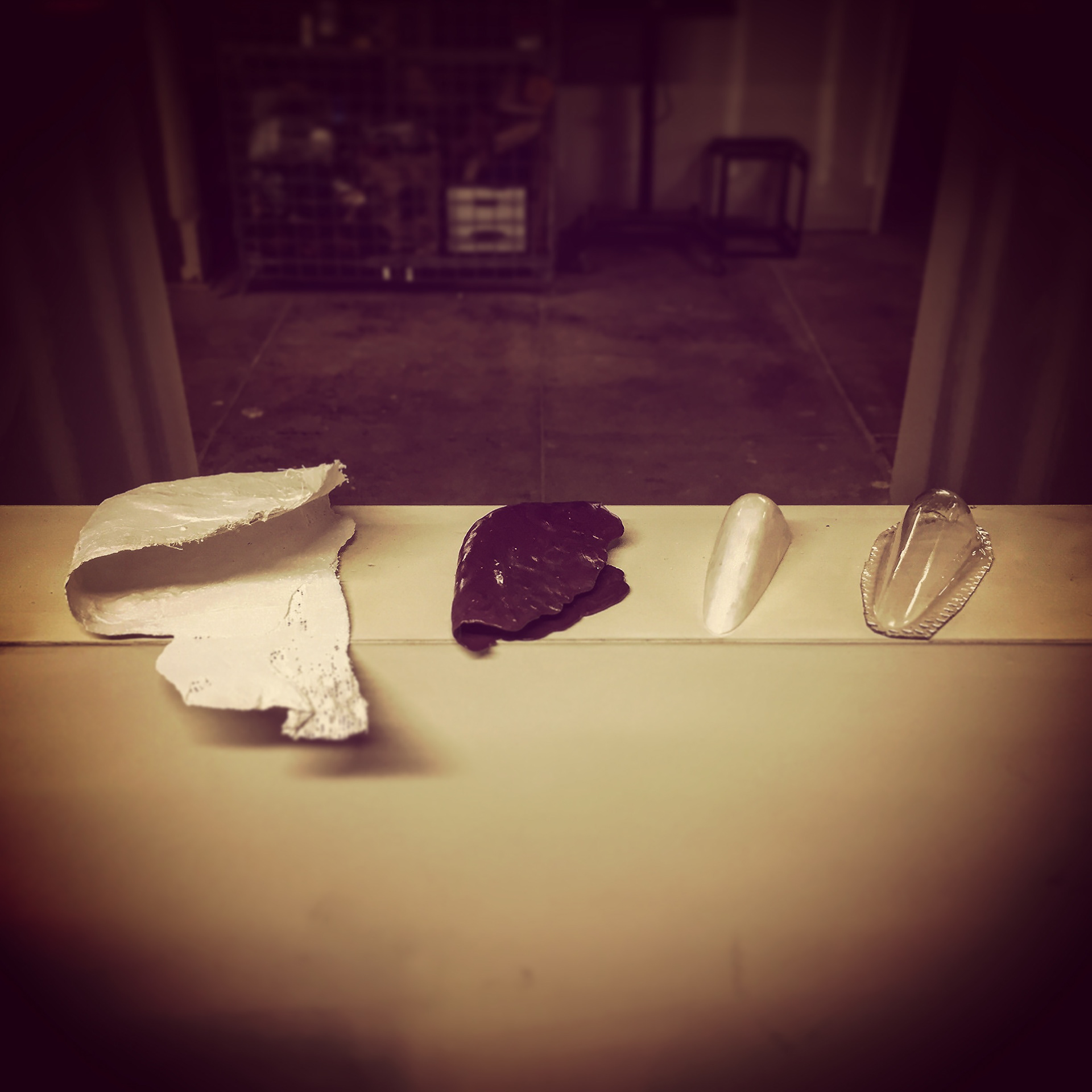
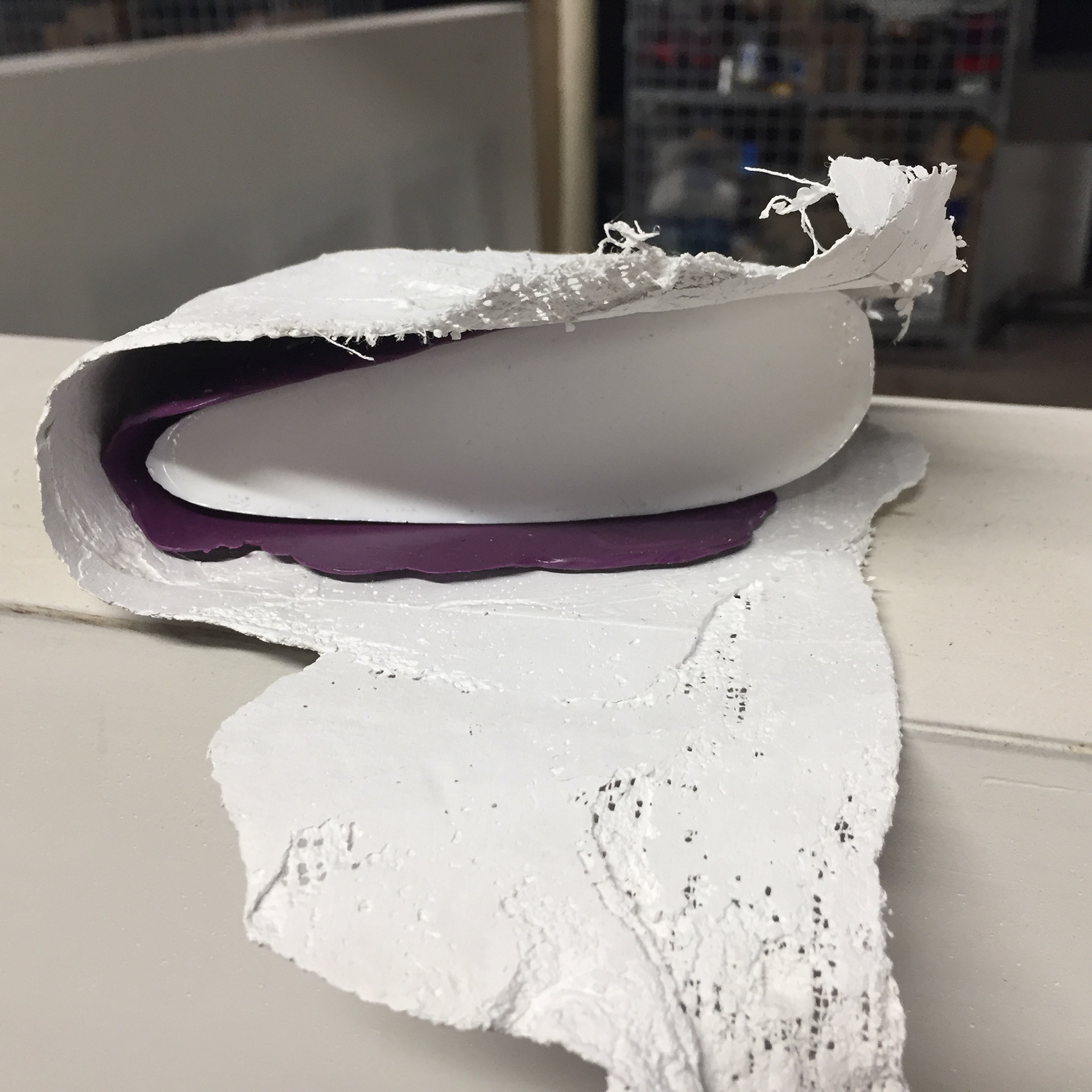
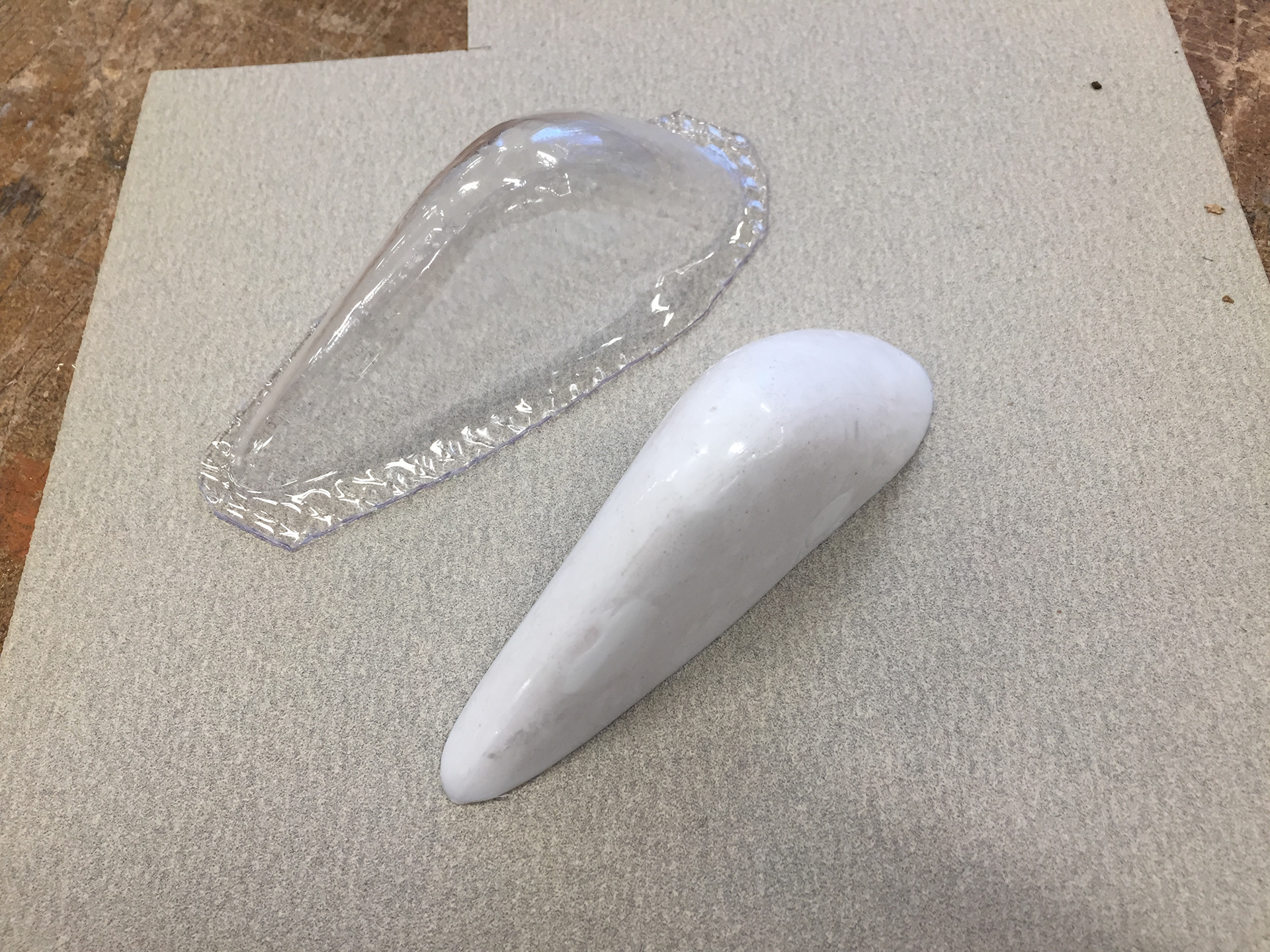
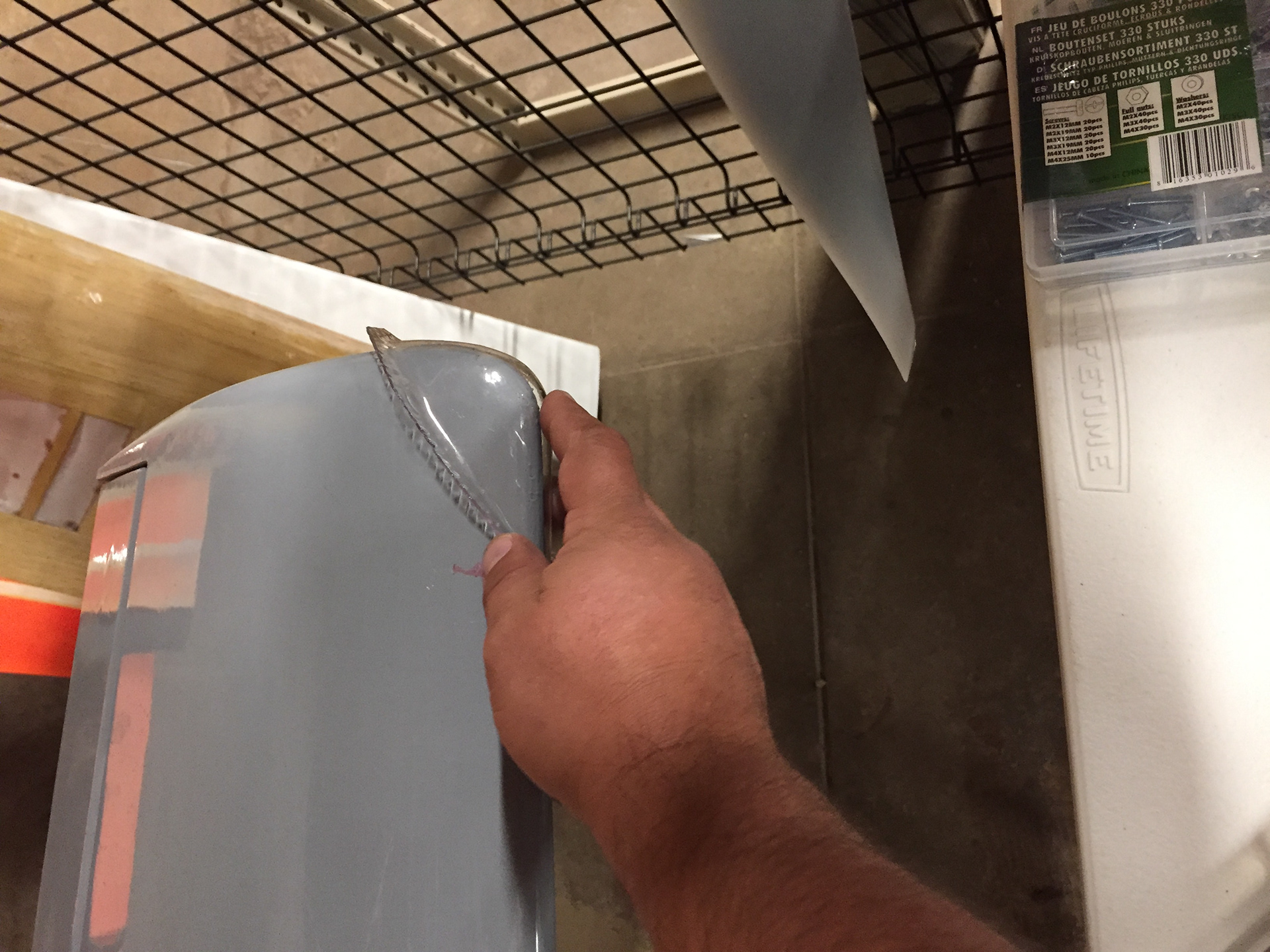
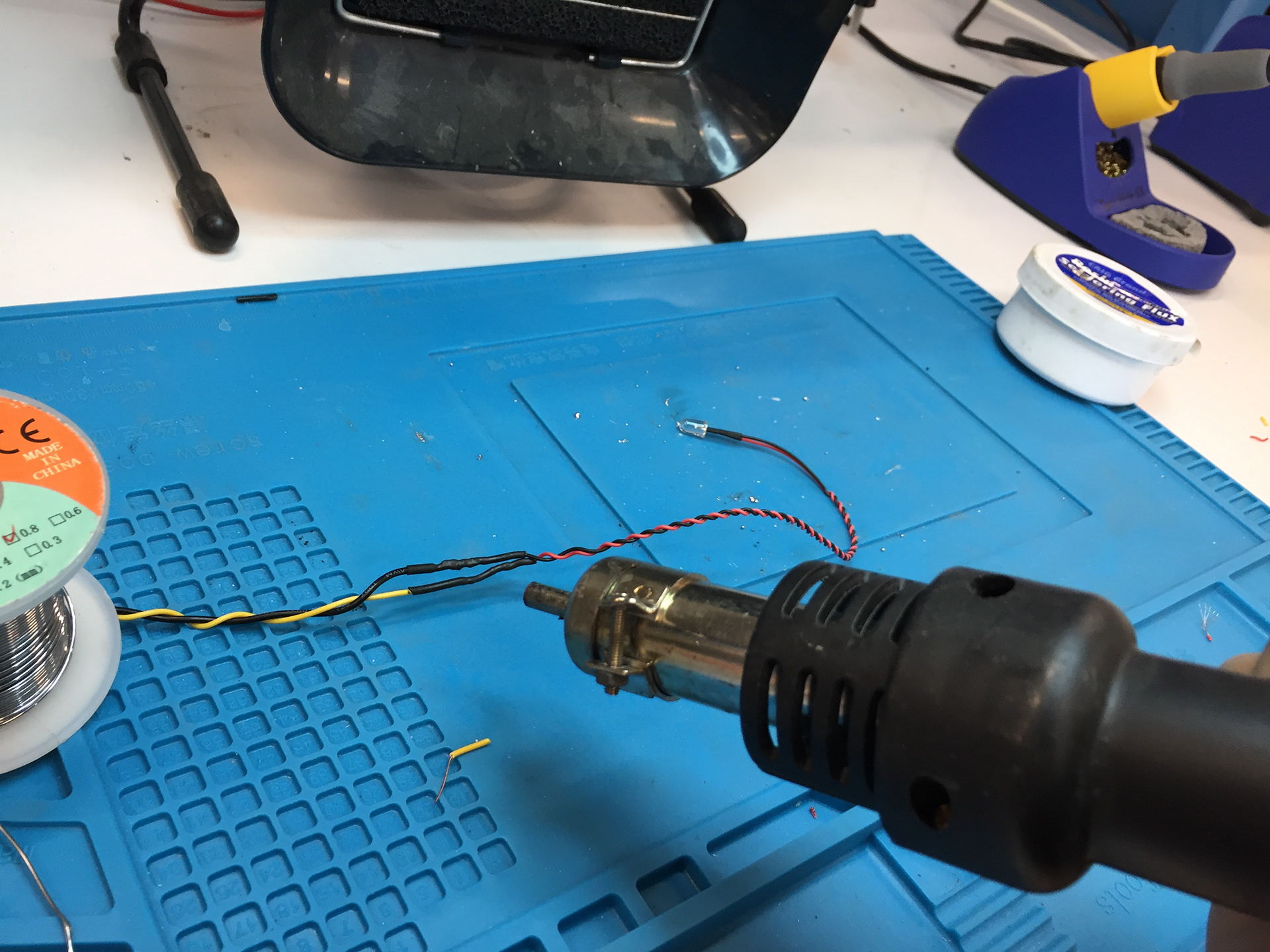
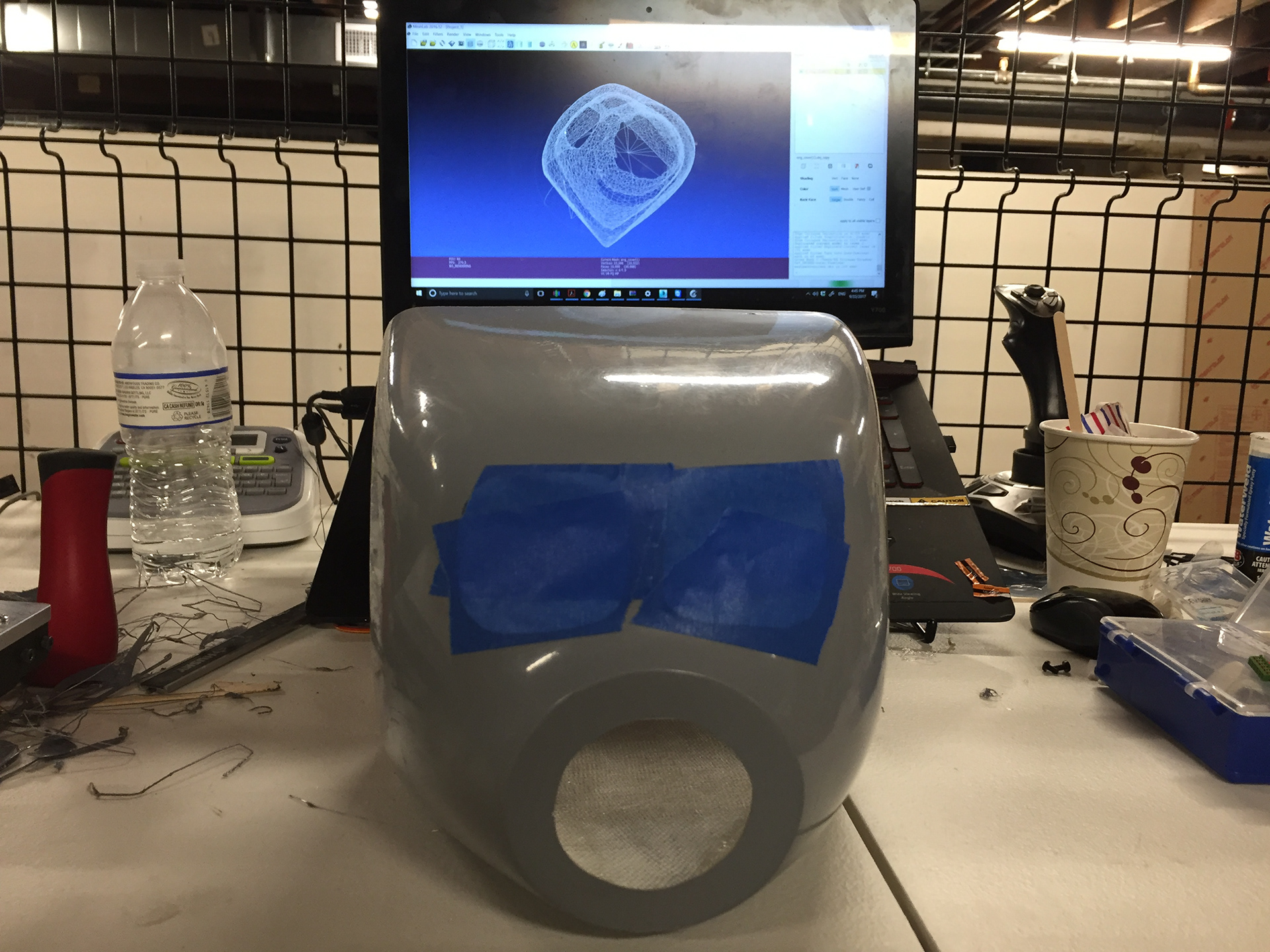
Cowling modification through 3d scanning and CAD
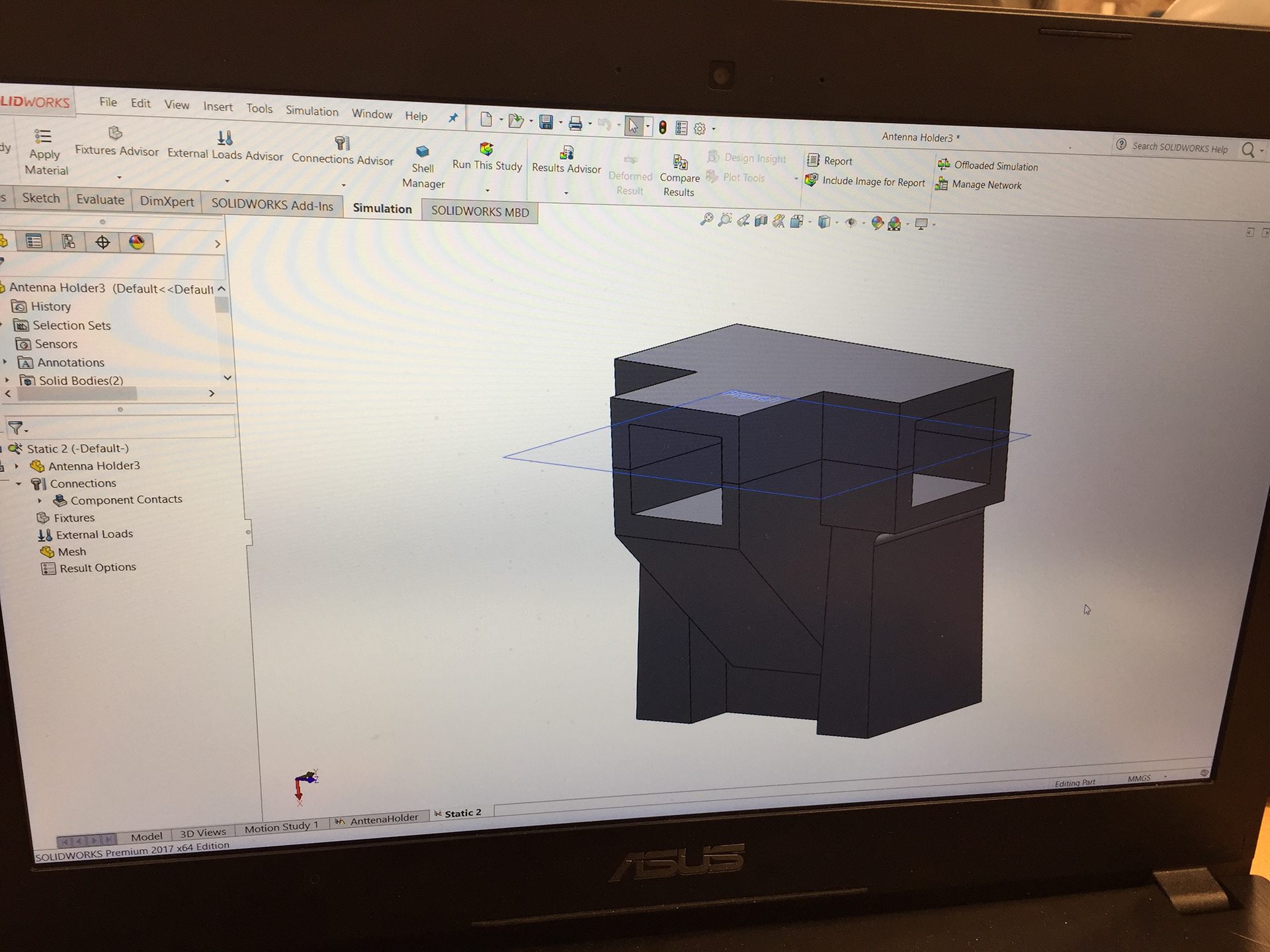
Rapid concept validation
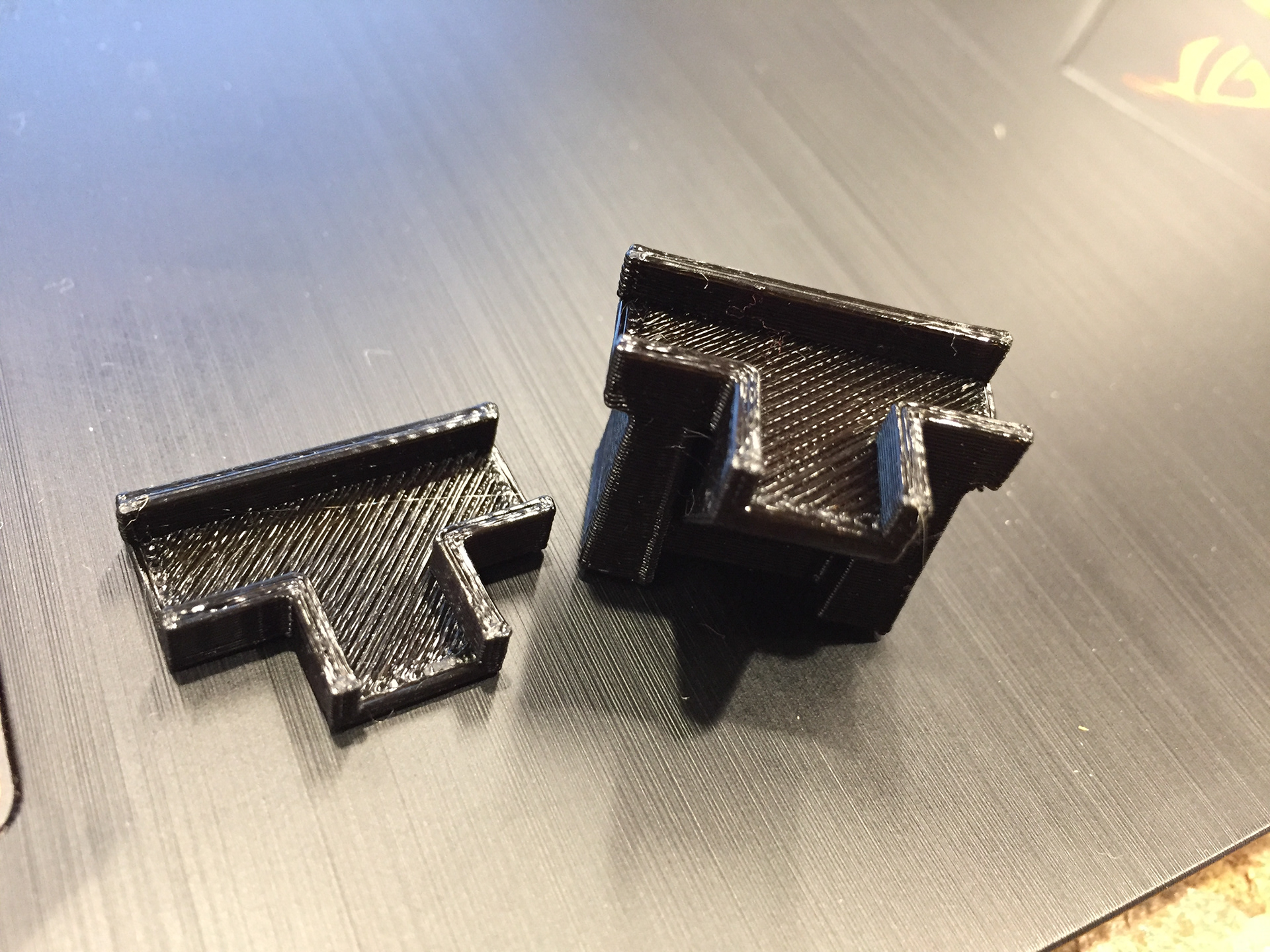
Antenna Holder
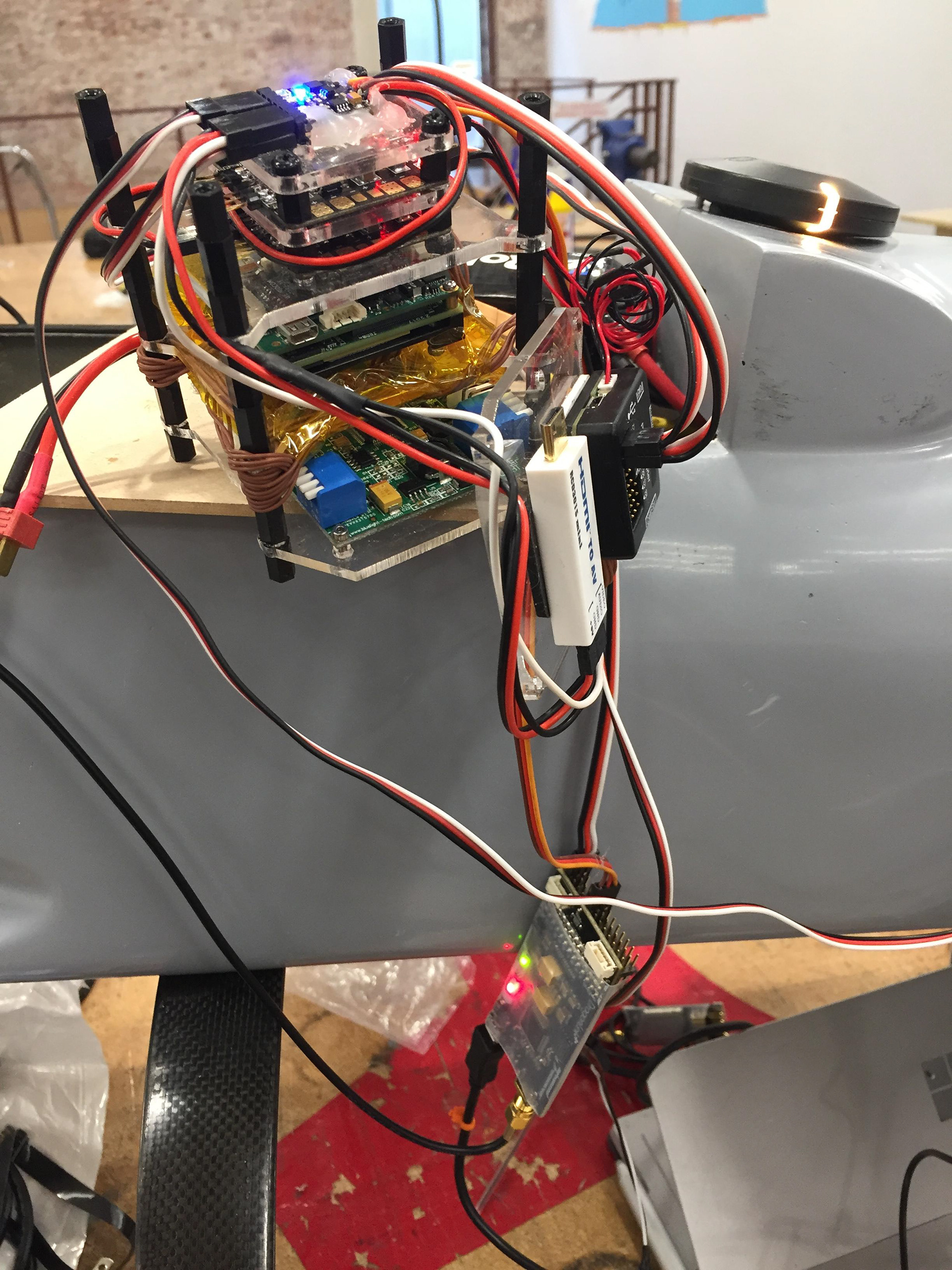
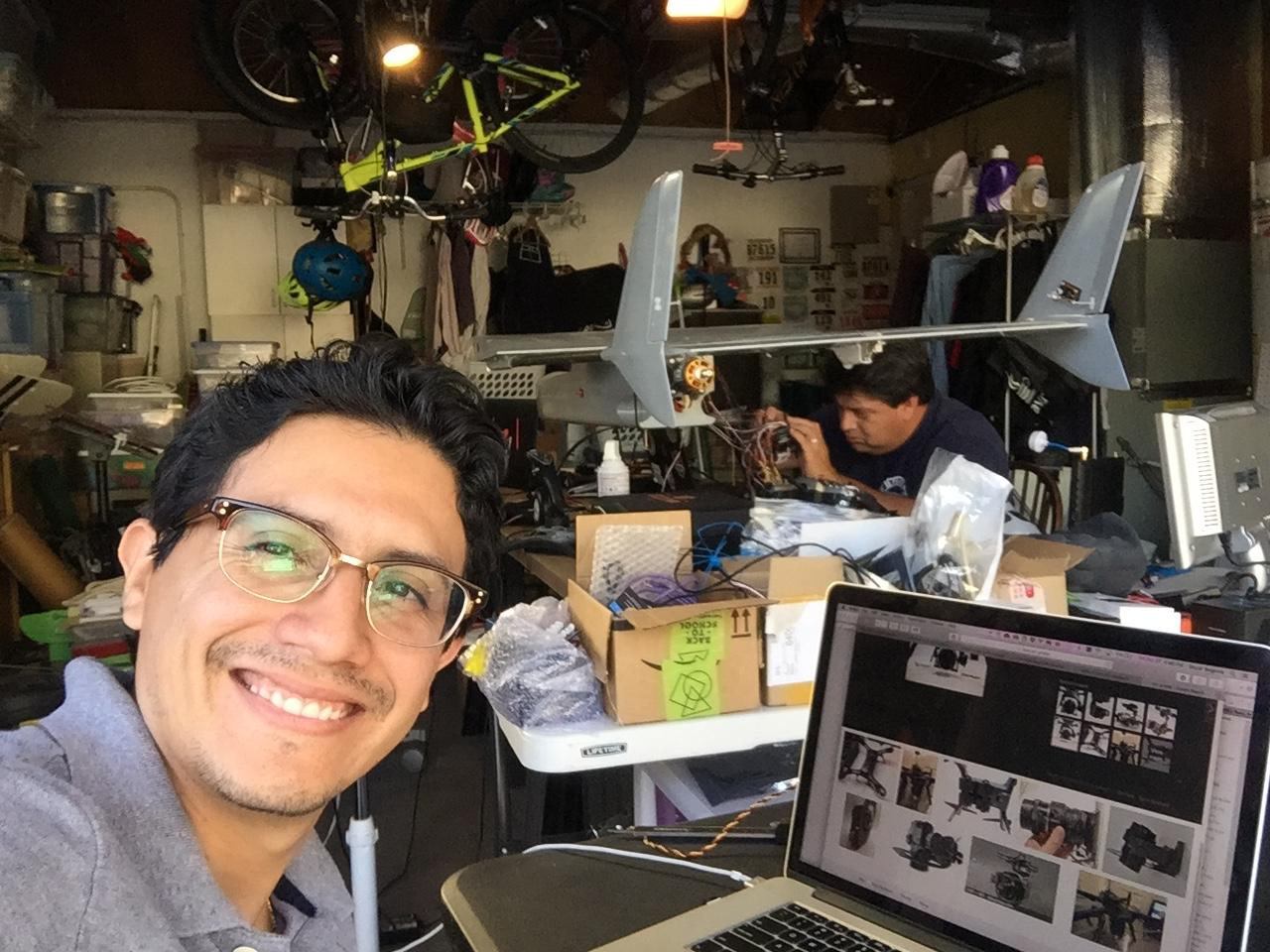
Design research
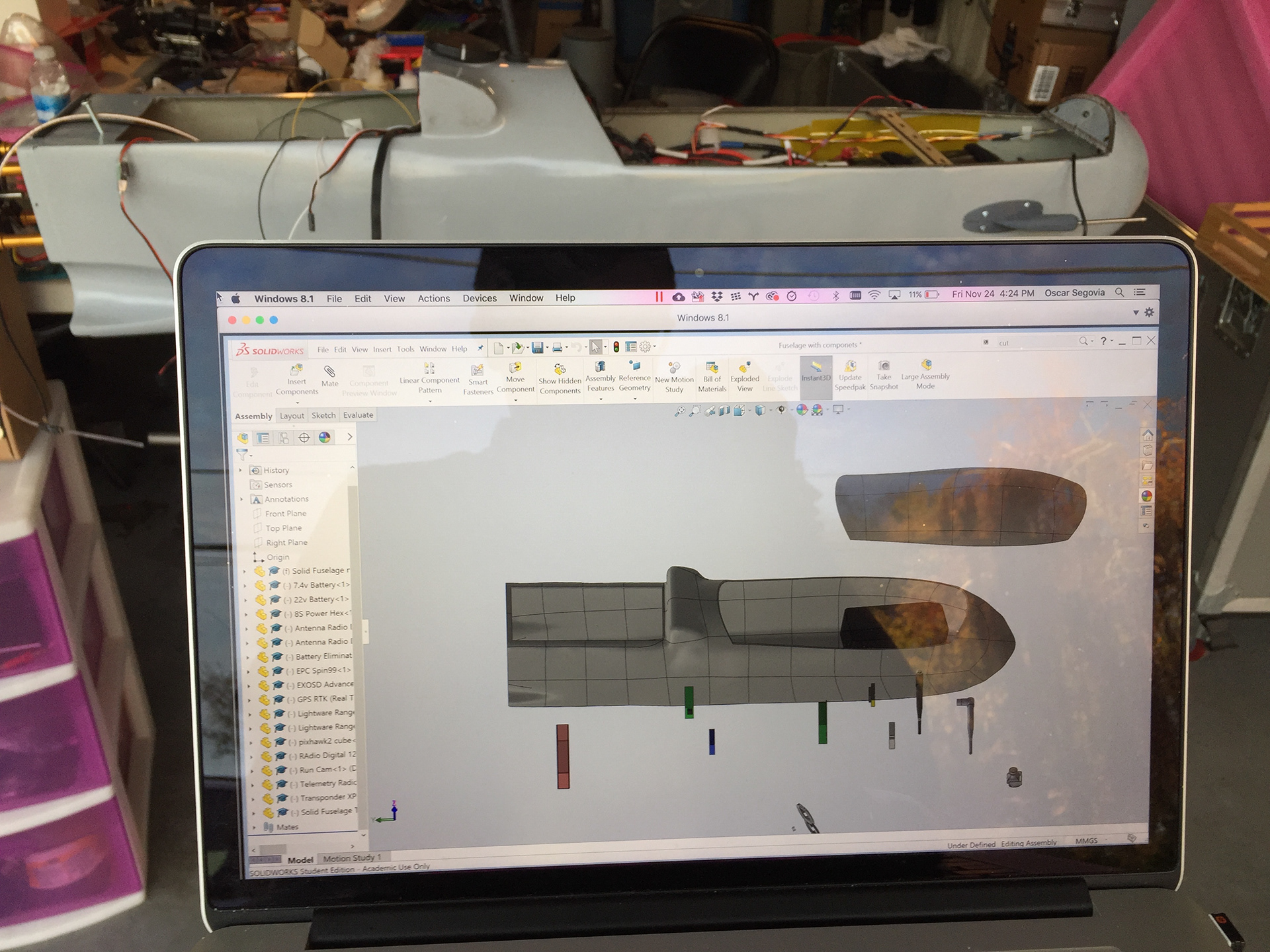
Virtual Integration of components to understand weight distribution and space constrains. 3D scan of plane into solid plus re-engineered off the shelf components