Utilizing Rapid Prototyping in the Creation of an Augmented Reality Headset
At startups the technical challenges are many. In order to raise money and continue towards the path of innovation, aside from a solid business model, iterations that demonstrate capability to move forward are essential. This is a small example of one step taken to move ahead in the race to create a commercially available AR headset.
----------------
Aurora AR was accepted into 2016's HTC ViveX Accelerator batch following this work and that of the entire team.
----------------
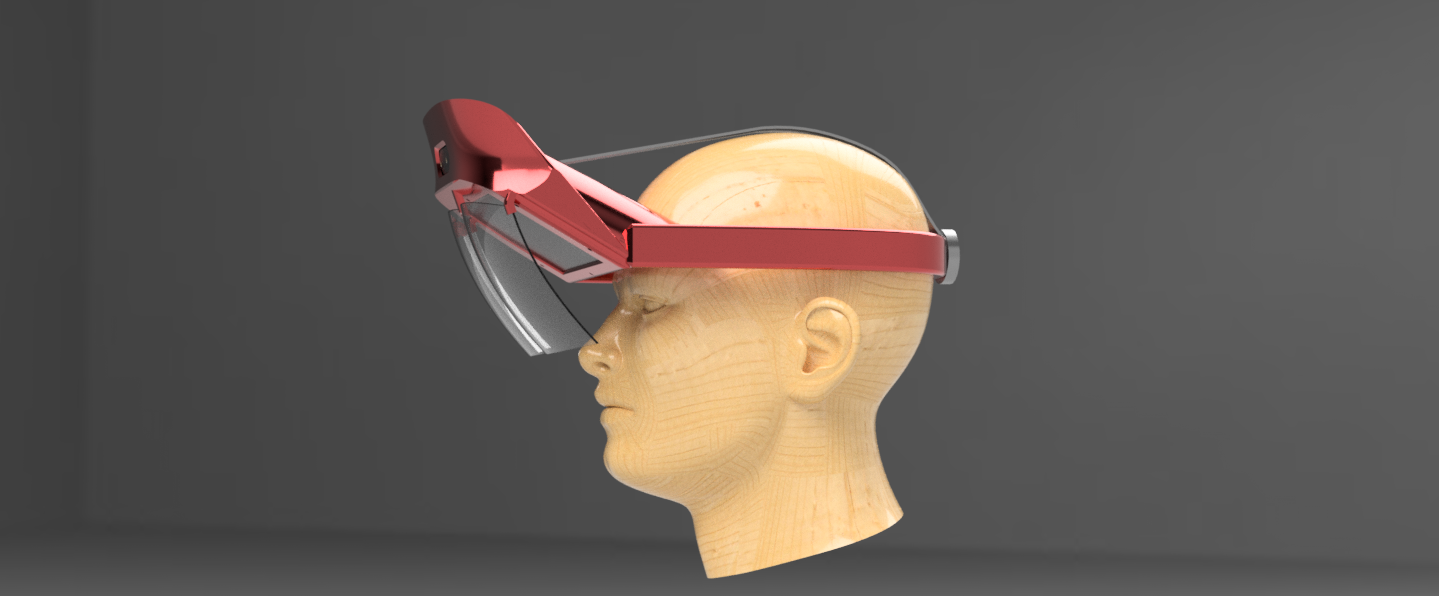
Failing fast and often in order to learn from the failures and achieve milestones is a necessary step towards innovation. The environment in which hardware startups operate is difficult, plagued with technological intricacies and strong competition.
However, investors are always looking for the next gold rush. AR so happens to be one of those areas of business with a lot of future possibilities to create valuable technology and Aurora AR is one of these companies playing the long game. As part of the initial team, I was tasked with creating the second iteration prototype in order to provide content for investor purposes as well as to identify future challenges and opportunities in the technical realm. Finally, I provided support in future relations with technical partners.
Skills utilized:
Solidworks, Fusion 360 - Solid and Surface Modeling
SLS with NYLON for 3D printed enclosure.
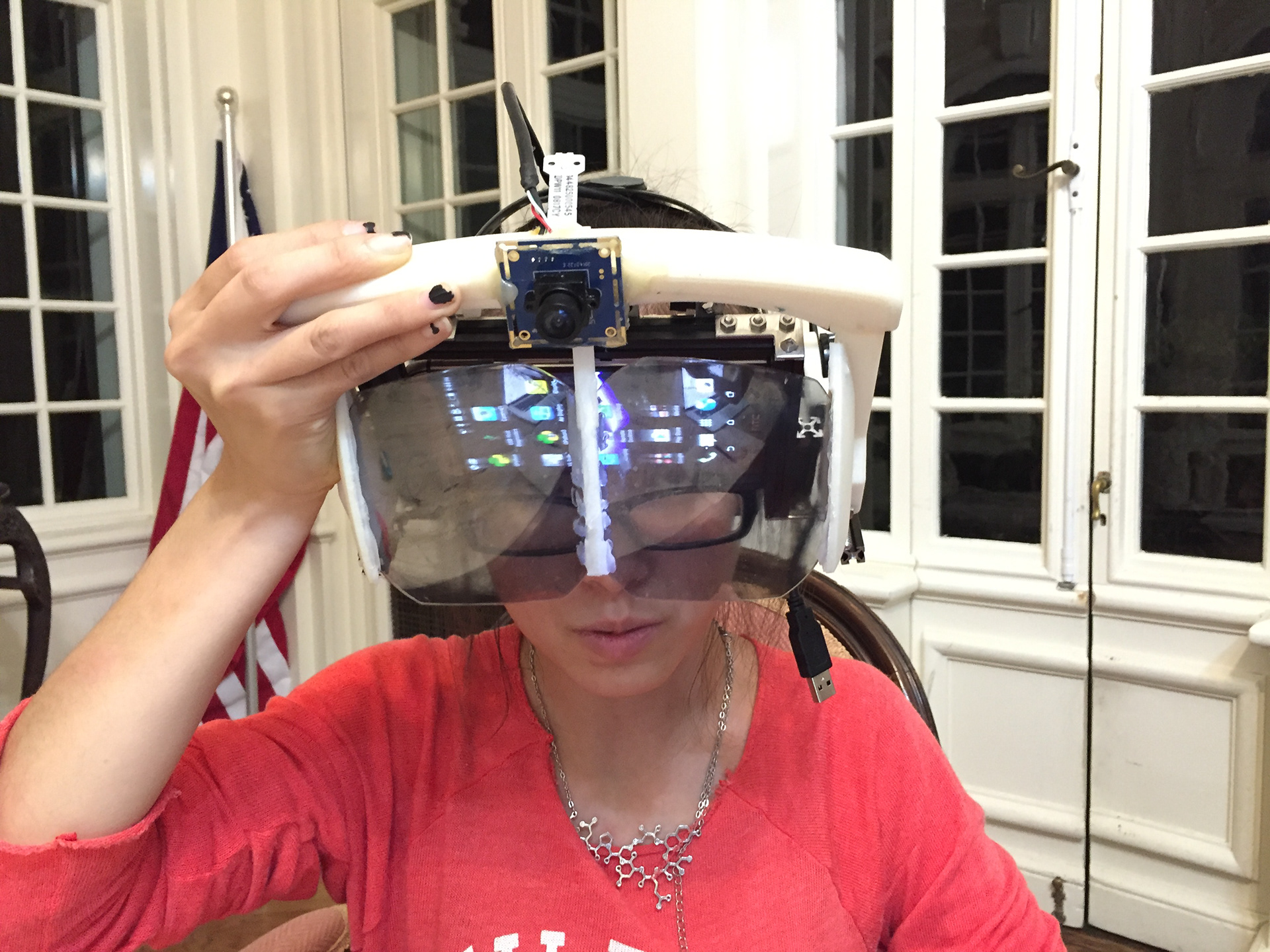
Original first iteration with custom made lenses and phone utilized as display
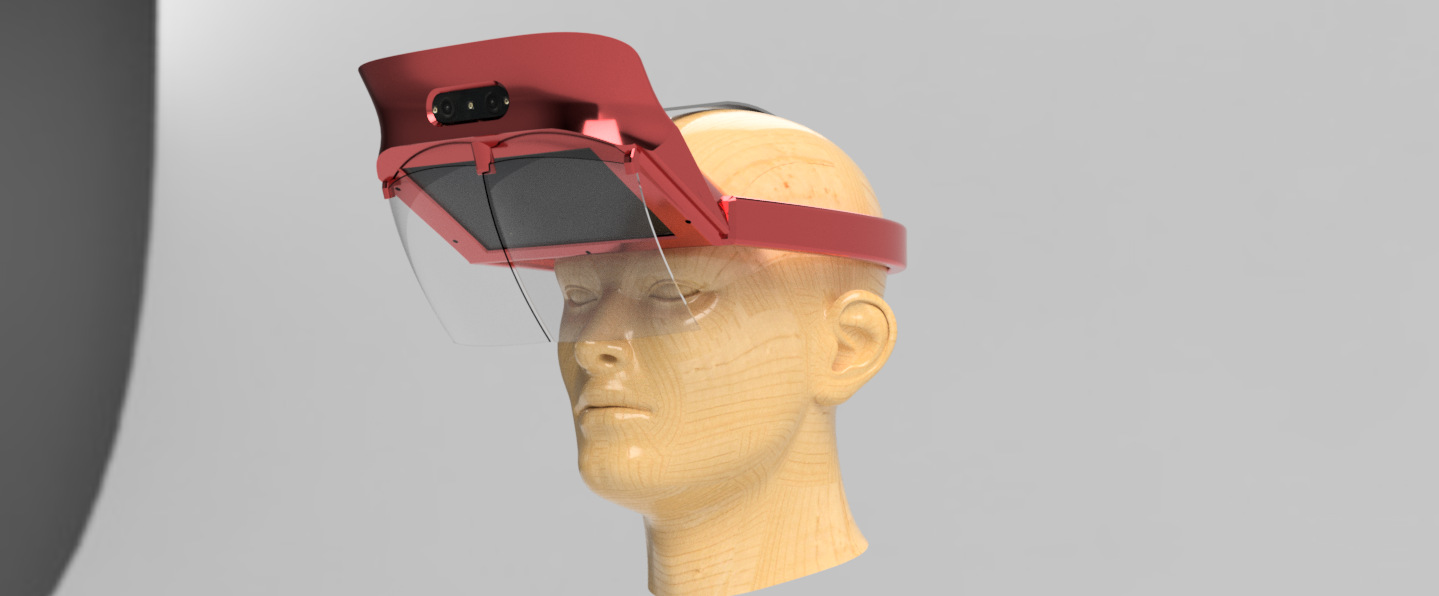
Render of Second Iteration utilizing the first prototype custom lenses.
One of the many items utilized as entry documents to HTC's Vivex Accelerator
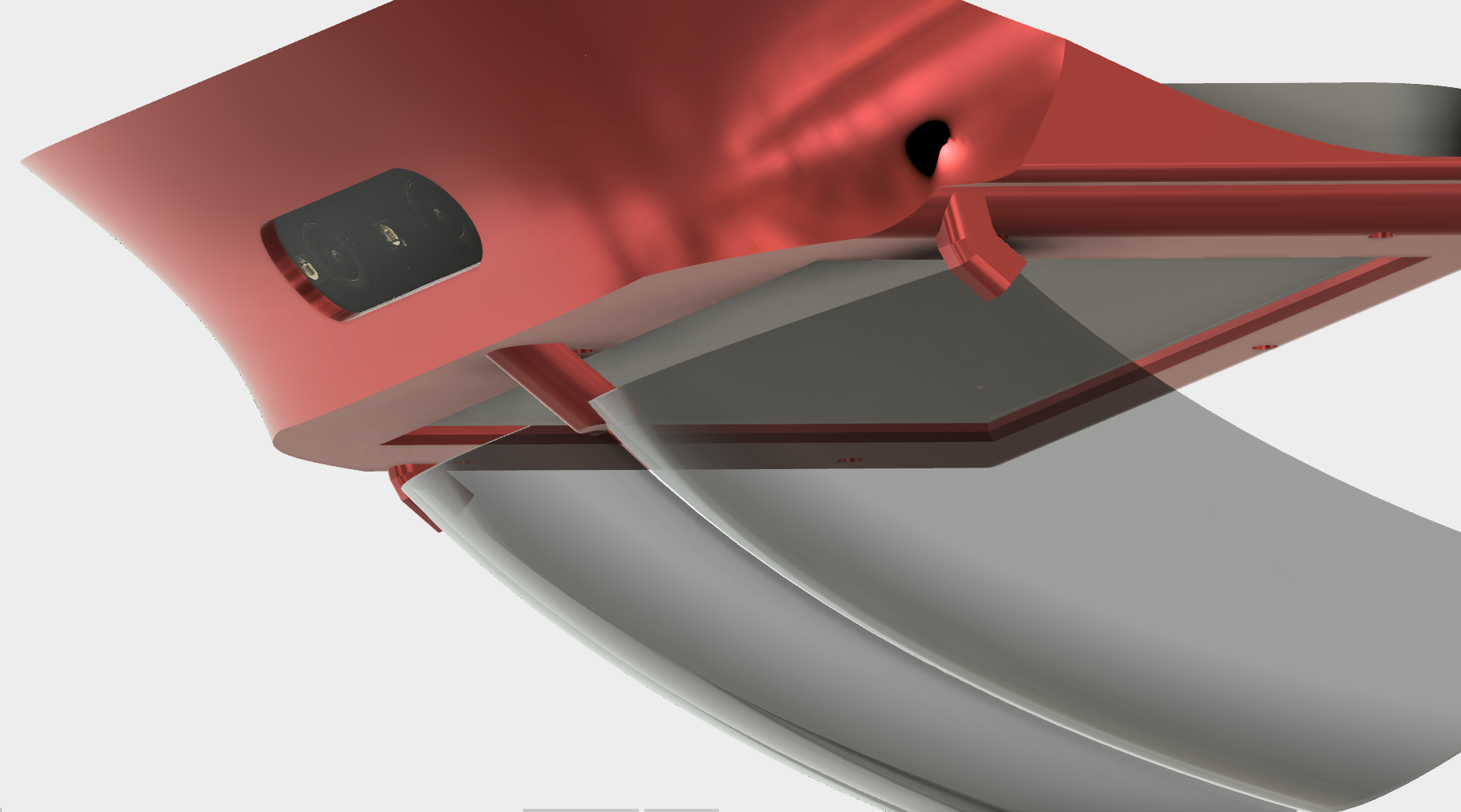
Special angle allows to visualize entire LCD screen on custom lenses while the custom camera collects visual information from the real world to render location specific images.
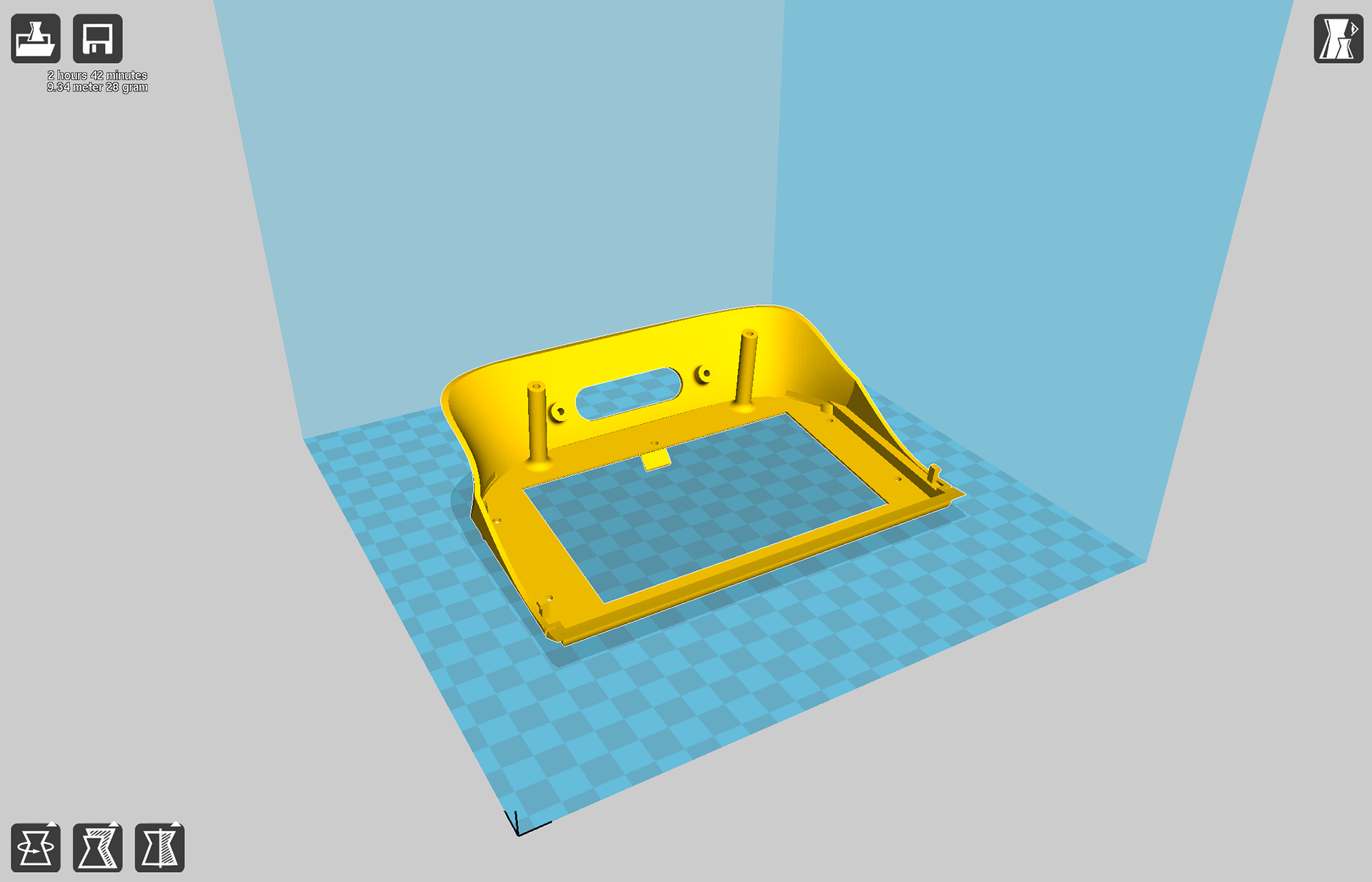
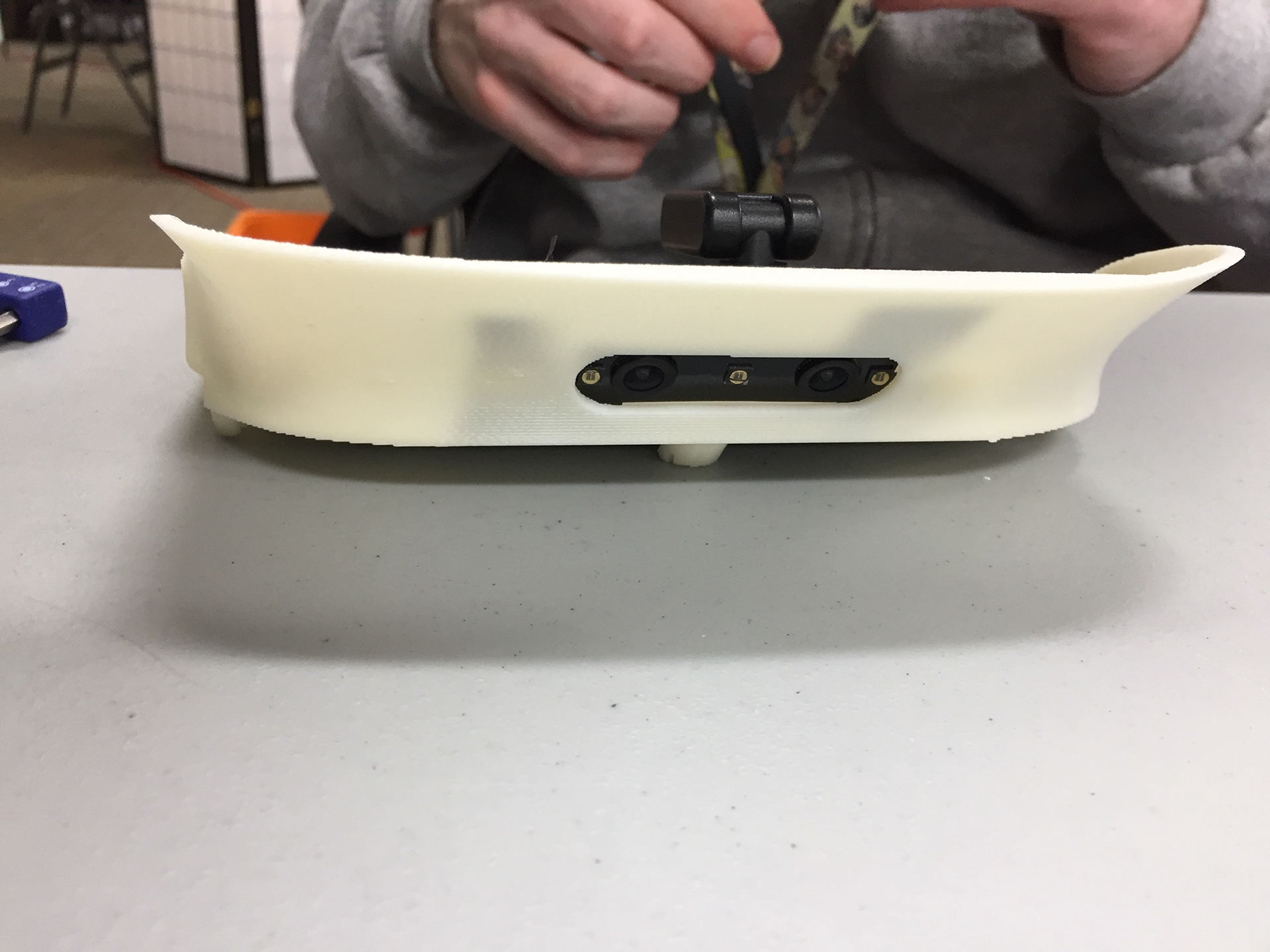
Fitting internal components for 2nd iteration works like looks like.
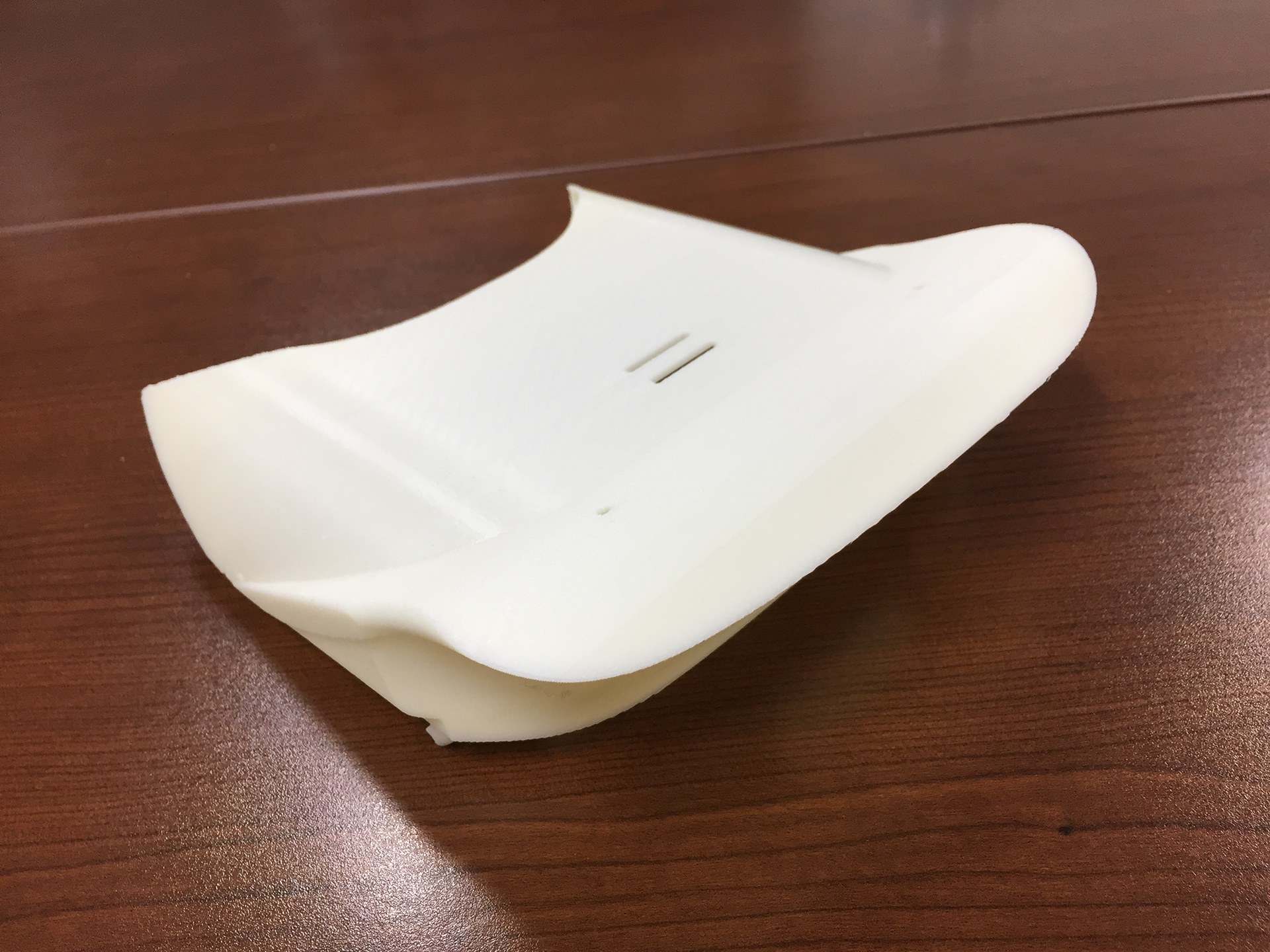